Зенкование и зенкерование отверстий — Сверление металла
Зенкование и зенкерование отверстий
Категория:
Сверление металла
Зенкование и зенкерование отверстий
Зен кованием называется обработка входной или выходной части отверстия с целью снятия фасок, заусенцев, а также образования углублений под головки болтов, винтов и заклепок. Инструменты, применяемые для этой цели, называются зенковками. По форме режущей части зенковки подразделяют на конические и цилиндрические.
Конические зенковки предназначены для снятия заусенцев в выходной части отверстия, для получения конусных углублений под головки потайных винтов, заклепок и центровых углублений при обработке деталей в центрах. Наибольшее распространение получили конические зенковки с углом конуса при вершине 2ср, равным 30, 60, 90 и 120°.
Цилиндрические зенковки с торцовыми зубьями применяются для обработки углублений под головки болтов, заклепок, шурупов, под плоские шайбы, а также для подрезания торцов, плоскостей бобышек, для выборки уступов и углов.
Зенкерованием называется обработка (расширение) предварительно просверленных штампованных или литых отверстий с целью придания им строгой цилиндрической формы, достижения большей точности и чистоты поверхности. Зенкерование обеспечивает получение отверстий 4—5-го класса точности. Отверстия 2—3-го класса точности получаются развертыванием. Поэтому к зенкерованию прибегают преимущественно как к промежуточной операции между сверлением и развертыванием.
Зенкерованием обрабатываются также литые, штампованные и прошитые отверстия.
Зенкеры отличаются от сверл устройством режущей части и большим числом режущих кромок. Большое
количество направляющих ленточек обеспечивает правильное и более устойчивое положение зенкера относительно оси обрабатываемого отверстия, а распределение усилий на три-четыре режущие кромки — более плавную, чем при сверлении, работу и получение чистого и достаточно точного отверстия.
По конструкции зенкеры бывают цельные (рис. 2, а), насадные (рис. 2,б) и со вставными ножами (рис. 2, в), а по Количеству зубьев (перьев) —трех- и четырехперые.
Рис. 2. Зенкеры: а —цельный; б—насадной; в—со вставными ножами
Цельные зенкеры имеют три или четыре режущие кромки, а насадные — четыре режущие кромки. Для обработки отверстий диаметром 12—20 мм применяют цельные зенкеры. Насадные зенкеры используют при обработке Отверстий диаметром свыше 20 мм. Сменные [(насадные) зенкеры соединяются с оправкой с помощью выступа на оправке и выреза на торце зенкера.
Зенкование и зенкерование выполняют на сверлильных станках и при помощи электрических или пневматических машинок. Крепление зенкеров аналогично креплению сверл.
—-
Очень часто приходится делать в верхней части отверстия конусное углубление большего диаметра, чем
диаметр самого отверстия. Такая операция называется зенкованием. Она необходима для того, например, чтобы головки винтов не выступали над поверхностью детали. Зенкуют отверстия с помощью специальных инструментов — зенковок. Режущая часть инструмента имеет коническую форму, поэтому и форма углубления тоже коническая.
Иногда отверстие зенкуют сверлом большего диаметра, чем то, которым сверлили отверстие,
Реклама:
Читать далее:
Развертывание и его применение
Статьи по теме:
Главная → Справочник → Статьи → Блог → Форум
Технология зенкования и зенкерования отверстий
Зенкерование отверстий представляет собой процесс обработки предварительно подготовленных (сверлением, литьем или штамповкой) отверстий с целью выполнения их геометрической формы с точностью до 9-11 квалитета и получения значений шероховатости поверхности в пределах от 1,25 до 2,5 мкм. Эту операцию выполняют на этапе механической обработки, предшествующем развертыванию отверстий. Зенкерование производят с применением специальных инструментов, зенкеров, установленных в патроны сверлильных станков.
Отверстие в заготовке, подлежащее зенкерованию, должно иметь соответствующий припуск на обработку инструментом. Величина припуска зависит от размера внутреннего диаметра отверстия. Например, для линейки диапазонов отверстий с размерами 5…24 мм, 25…35 мм, 36…45 мм требуется наличие в них припусков на обработку, размеры которых равны, соответственно, 1.0, 1.5, 2.0 миллиметра.
Зенкер отличается от сверла своей конструкцией и формой режущих кромок. Инструмент имеет в наличии три или четыре конструктивных элемента – зуба, которые обеспечивают максимально точное совмещение осей инструмента и отверстия, а также устойчивое положение инструмента в заданной позиции.
Для выполнения отверстий цилиндрической формы в заготовках применяют цилиндрические зенкеры. Другой инструмент, конические, у которых угол при вершине равен 60, 75, 90 и 120 градусов, предназначен для выполнения углублений конической формы. Для обеспечения большой точности совмещения оси отверстия в заготовке и оси выполненного инструментом цилиндрического отверстия в зенкерах имеется направляющая цапфа. Режим резания (скорость и частоту вращения инструмента) выбирают с обязательным учетом состава материалов, из которых изготовлены заготовка и зенкер.
Зенкование отверстий – это операция технологического процесса обработки углублений цилиндрической или конической формы, а также фасок, предназначенных для установки в готовые отверстия крепежных деталей, таких, как болты, винты или заклепки с потайными головками (с потаем). Операцию зенкования, как и зенкерования, отверстий выполняют на сверлильных станках с использованием зенковок и сверл с диаметрами, превышающими по размеру диаметры отверстий. Для обеспечения максимально точного совмещения оси отверстия и углубления под потайную головку крепежной детали на зенковках присутствуют конструктивные элементы – направляющие цапфы и режущие зубья.
Товары каталога:
Please enable JavaScript to view the comments powered by Disqus.

Зенкерование зенкование цекование отверстий
Обработка зенкерами отверстий в деталях, изготовленных методами литья, штамповки или сверления, используется тогда, когда необходимо существенно снизить степень шероховатости поверхности, а также ликвидировать такие дефекты, как эллипсность, овальность и пр.
В отличие от сверл, такой режущий инструмент, как зенкер, имеет более двух режущих поверхностей (обычно – три или четыре, а довольно часто и более), и поэтому с его использованием можно получить отверстия, имеющие не только хорошее качество поверхности, но и высокую точность геометрических размеров в той части. которая касается диаметра. Зенкеры не имеют перемычек между рабочим поверхностями, что обеспечивает их повышенную жесткость при обработке.
В ходе зенкерования скорость подач в несколько раз больше, чем скорость сверления, и поэтому во многих случаях для увеличения исходного диаметра отверстий этот технологический процесс предпочтительнее, чем рассверливание.
В подавляющем большинстве случаев при механической обработке деталей операция зенкерования производится после сверления и перед развертыванием. По этой причине в каждом конкретном случае диаметр зенкера подбирается таким, чтобы он был несколько меньше того, который должно иметь отверстие в итоге (разница называется в технике припуском на развертывание).
Для изготовления зенкеров чаще всего используется инструментальная углеродистая сталь У12А, легированная сталь 9ХС или быстрорежущая сталь Р9.
С точки зрения конструкции
В тех случаях, когда необходимо обрабатывать отверстия, имеющие диаметры от 12 до 20 миллиметров, используются цельные зенкеры. Они имеют или три, или четыре режущие кромки (последний вариант – со вставными пластинами).
Если технологический процесс изготовления деталей предполагает обработку отверстий, имеющих диаметр более 20 миллиметров, то используются зенкеры со вставными пластинами. Эти режущие части инструмента соединяются с оправкой при помощи специальных вырезов и выступов. В промышленности сейчас используются зенкеры, которые имеют до восьми и более режущих поверхностей.
Для того чтобы обеспечить выполнение нескольких операций зенкерования одновременно, используются комбинированные зенкеры. Они бывают ступенчатыми или сборными, причем последние нередко комбинируются с инструментами других видов: развертками, сверлами, расточными пластинами и т.п.
Цекование отверстий
Цекование представляет собой технологическую операцию, с помощью которой крепежные отверстия обрабатываются таким образом, чтобы обеспечить получение опорных поверхностей под винты.
Для этого используются цековки. Они представляют собой насадные головки, снабженные цилиндрическими выступами, обеспечивающими должное направление режущего инструмента, и имеющие торцевые зубцы.
Цековки, имеющие небольшие размеры, выпускаются, как правило, хвостовыми, а имеющие размеры достаточно значительные – насадными. Чтобы точно направить их в соответствующие отверстия, используются цапфы, а сам режущий инструмент изготавливается из быстрорежущей стали и нередко оснащается пластинами из твердых сплавов.
Зенкование отверстий
В технике под зенкованием подразумевается технологическая операция, состоящая в снятии фасок с уже готовых отверстий, удалении заусенцев, получении отверстий определенной конфигурации на основе уже имеющихся.
Технологическая операция зенкования осуществляется при помощи такого инструмента, как зенковки. Для обработки опорных поверхностей под крепежные винты они делаются или со съемной цапфой, или цельными, а что касается размеров, то в каждом конкретном случае они подбираются технологами металлообрабатывающего производства отдельно.
§ 13. Развертывание, зенкерование и зенкование
Развертывание. Для получения
отверстий с чистой поверхностью или для точной подгонки отверстия под
шлифованную деталь производят операцию, которая называется развертыванием.
Развертывание выполняют вручную или на сверлильном станке с помощью разверток.
Ручные развертки приводятся во вращение ручным воротком.
Развертки бывают цилиндрические (рис. 28 а, б) и конические (рис. 28, в). Конические развертки предназначены для развертывания конусных отверстий.
Рис. 28. Развертки: а — цилиндрическая ручная, б — то же, машинная, в —коническая
На рабочей части развертки имеется от 6 до 14 нарезанных зубьев, вдоль которых расположены канавки; зубья служат для образования режущих кромок и отвода наружу снимаемой стружки. Нижняя конусная часть развертки снимает стружку, а верхняя — калибрующая— направляет развертку и окончательно калибрует отверстия.
Для более чистой обработки
поверхности отверстий и охлаждения инструмента при развертывании просверленные
отверстия в стали смазывают минеральным маслом, в меди — эмульсией, в алюминии
— скипидаром, а в латуни и бронзе отверстия развертывают без смазывания.
Отверстия развертывают вручную следующим способом. Деталь прочно укрепляют в тисках. В отверстие детали вставляют развертку, чтобы ось развертки совпала с осью отверстия. Затем начинают вращать вороток с разверткой вправо, плавно подавая его вперед. Развертку вращают только в одну сторону.
Зенкерование и зенкование. Зенкерование — это обработка отверстия, полученного при литье, ковке или штамповке, для придания ему цилиндрической формы, требуемого размера и получения чистой поверхности. Зенкерование — промежуточная операция при обработке отверстия под развертку, выполняемая зенкером. Зенкером обрабатывают также конусные и цилиндрические углубления с плоским дном. Операцию зенкерования выполняют так же, как и развертывание.
Зенкер (рис. 29, а) имеет большее число режущих кромок (три или четыре), чем спиральное сверло, и обеспечивает большую чистоту обработки отверстия.
Рис. 29. Зенкер (а),
коническая (б) и цилиндрическая (в) зенковки
Припуск под зенкерование для отверстий диаметром от 15 до 35 мм дается 1—1,5 мм.
Зенкование — это обработка выходной части отверстия (снятие заусенцев) для получения конических или цилиндрических углублений под потайные головки заклепок и винтов. Зенкование выполняют конической или цилиндрической зенковкой (рис. 29,б,в).
Операции зенкования производят на сверлильном станке, как и сверление отверстий на требуемую глубину,
Зенкование и зенкерование — Энциклопедия по машиностроению XXL
Зенкование и зенкерование выполняют на сверлильных станках и при помощи электрических или пневматических машинок. Крепление зенкеров аналогично креплению сверл. [c.234]Операции зенкования и зенкерования в сущности напоминают операцию сверления. [c.156]
Операции зенкования и зенкерования выполняют многолезвийными инструментами, называемыми зенкерами.
[c.156]
Небольшие изделия при зенковании и зенкеровании необходимо прочно зажимать в тисках, а большие притягивать к столу планками. Небольшие конические потаи можно зенковать, удерживая изделие в руках. [c.158]
Скорость резания при зенковании и зенкеровании должна быть примерно в полтора раза меньше, чем при сверлении сверлом такогО же диаметра. Цилиндрическими зенкерами диаметром до 20 мм работают при оборотах, не превышаюш,их 250 в минуту при работе зенкерами, диаметром свыше 20 мм числа оборотов должны быть снижены до 100—150 в минуту. [c.158]
При зенковании и зенкеровании необходимо соблюдать те же правила техники безопасности, что и при сверлении. [c.158]
Зенкование и зенкерование, как и процесс сверления, происходят при двух одновременных движениях инструмента — вращательном и поступательном вдоль оси. Диаметр сверла, выбираемого для сверления отверстия под обработку зенкером, должен быть меньше диаметра окончательно обработанного отверстия на величину припуска. Ниже приведены припуски (на сторону) на зенкерование после сверления отверстия.
[c.129]
ЗЕНКОВАНИЕ И ЗЕНКЕРОВАНИЕ ОТВЕРСТИЙ [c.72]
Зенкование и зенкерование выполняются обычно на сверлильных станках. Поскольку зенкер имеет больше режущих кромок, чем сверло, увеличивается точность обработки. [c.75]
Всех слесарей объединяет единая технология выполнения операций, к которым относятся разметка, рубка, правка и гибка, резание металлов, опиливание, сверление, зенкование и зенкерование, развертывание отверстий, нарезание резьбы, клепка, шабрение, распиливание и припасовка, притирка и доводка, пайка, лужение и склеивание. [c.6]
При сверлении, зенкеровании, цековании, зенковании и центровании стальных деталей скорость резания определяется по формуле [c.87]
Технология зенкерования, цекования, зенкования и развертывания [c.239]
На сверлильных станках, кроме сверления и рассверливания отверстий, можно выполнять операции зенкерования, цекования, зенкования и развертывания.
[c.239]
Работы, выполняемые на токарных станках. Токарные станки являются наиболее универсальными из всех видов металлорежущего оборудования. На них можно производить разнообразные работы обтачивать, растачивать цилиндрические (рис. 12.6, а и б), конические и фасонные поверхности вращения, подрезать торцы (рис. 12.6, в) и соответственно обрабатывать плоскости, прорезать канавки, нарезать резцом крепежные и ходовые резьбы любого профиля. Кроме того, на токарных станках с помощью инструментов, устанавливаемых в пиноли задней бабки, можно производить сверление, зенкерование, зенкование и развертывание отверстий, расположенных соосно со шпинделем станка, а также нарезать внутренние и наружные крепежные резьбы с помощью метчиков и плашек. Точность и шероховатость, достигаемые на токарных станках, следующие при черновой обработке квалитеты 12-14 и Д =160 — 80 мкм при чистовой обработке квалитеты 9-10 и R =40-. 0 мкм при тонкой чистовой обработке алмазным инструментом квалитеты 6-7 и /г =1,25-0,63 мкм.
[c.363]
Зенкерование, зенкование и развертывание [c.198]
Слесарные работы состоят из разнообразных технологических операций, в которые входят разметка, рубка, правка и гибка металлов, резка металлов ножовкой и ножницами, опиливание, сверление, зенкерование, зенкование и развертывание, нарезание резьбы, клепка, шабрение, притирка, доводка н др. [c.477]
Режимы резания при зенковании и цековании те же, что и при зенкеровании. [c.160]
При работе на сверлильных станках расчет основного (технологического) времени для сверления, рассверливания, зенкерования, развертывания, зенкования и подрезки торца цековкой или подрезной пластиной рассчитывается по формуле [c.247]
L —длина хода сверла, зенкера, развертки или зенковки в жл. Пои сверлении, развертывании и зенкеровании L = l- -y, при зенковании L = l-j-l (механическая подача), L = i (ручная подача)
[c. 787]
Сверление, зенкерование, зенкование и развертывание отверстий выполняют соответствующими инструментами, закрепляемыми в пиноли задней бабки. [c.454]
ЗЕНКЕРОВАНИЕ, ЗЕНКОВАНИЕ И РАЗВЕРТЫВАНИЕ [c.340]
Рекомендуемые скорости резания. При сверлении и зенкеровании стали, а также цековании и зенковании стали и чугуна скорость резания [c.198]
Высокая производительность радиально-сверлильных ставков достигается при оснащении их специальными приспособлениями. Эти станки позволяют производить сверление, рассверливание и зенкерование предварительно просверленных отверстий, зенкование торцовых поверхностей, цилиндрических и конических углублений, развертывание отверстий, нарезание внутренней резьбы метчиками. [c.53]
Цекование производится зенкерами (цековками) для зачистки торцовых поверхностей. Цековками обрабатывают бобышки под шайбы, упорные кольца, гайки. Режимы резания при зенковании и цековании берут по тем же таблицам, что и при зенкеровании.
[c.281]
Зенкование и зенкерование лучше производить на сверлильном станке. Несколько хуже и труднее эти операции выполняются с помощью электро- или пневмодрели. Крепление зенкера ничем не отличается от крепления сверла, так как они имеют одинаковые хвостовики. [c.157]
Рассверливание, зенкерование, развертывание в упор, зенкование и цеко-вание [c.548]
Сверление, зенкерованне, развертывание, цекование, зенкование и нарезание резьбы метчиками выполняют на расточных станках так же, как и на вертикально-сверлильных. Инструмент закрепляют в расточном шпинделе и сообщают ему главное вращательное движение резания и движение осевой подачи. Заготовка, установленная на столе станка, остается неподвижной. [c.375]
Многие отверстия, особенно отверстия в стыковых поясах под клепку, а таклдополнительной обработке— рассверливанию, т. е. зенкованию и зеикерова-нию. Инструментом для зенкования являются зенковки, а для зенкерования — зенкеры.
[c.41]
Какая разница мелцентровых отверстий, образование углублений под потайные головки винтов и заклепок. Зенкерование— это обработка готовых отверстий, полученных отливкой, штамповкой или сверлением, для придания им строго цилиндрической формы, большей точности и лучшей чистоты обработки. После зенкера отверстие получается [c.41]
Этими основными видами работ не исчерпываются технологические возможности сверлильных станков, на которых можно, например, еще формовать головки обычных заклепок, разваль цовывать пустотелые заклепки, обрабатывать многогранные отверстия, а также выполнять другие операции. Но так как сверловщик 1—2-го разряда должен уметь выполнять ограниченный неречень операций, то ниже мы более подробно рассмотрим только операции сверления, рассверливания, развертывания, зенкерования, зенкования и нарезания резьб [c.150]
Характерным при.мером полуавто.матов с программным управлением является специальный координатносверлильный станок (рис. 89), применяемый на предприятиях радиопромышленности для сверления и зенкерования отверстий в платах радиотехнических устройств. Процессы сверления и зенкования отверстий на нем полностью автоматизированы и выполняются по заранее заданной программе, но загрузка и выгрузка каждой плиты производится вручную.
[c.158]
Сверление, зенкерование, зенкование и развертывание отверстий выполняют соответствующими инструментами, закрепляемыми в пиноли задней бабки. На рис. 1.33, ж показана схема сверления в заготовке цилиндрического отверстня. [c.452]
Скорости резания при зенкеровании стали и чугуна зенкерами из быстрорежущей стали, а также зенкерами, оснащенными твердыми сплавами приведены в табл. 62—64 и 66, а скорости резания при зенкованни и подрезании торцовых поверхностей — в табл. 67. [c.149]
Сверление, зенкование, зенкерование и развертывание при слесарных работах в автомобилестроении
Категория:
Автомобилестроение
Публикация:
Сверление, зенкование, зенкерование и развертывание при слесарных работах в автомобилестроении
Читать далее:
Сверление, зенкование, зенкерование и развертывание при слесарных работах в автомобилестроении
Сверлением называется процесс образования сверлом отверстии в сплошном материале. Сверлением достигаются 4—5-й классы точности и шероховатость.
Сверла по конструкции бывают спиральные и др. Наибольшее применение находят спиральные сверла, которые по форме хвостовика могут быть с цилиндрическим и коническим хвостовиком. Спиральные сверла изготавливают главным обра-30м из быстрорежущих сталей, для сверления чугуна и материалов повышенной твердости применяют спиральные сверла, оснащенные пластинками твердого сплава ВК8 или монолитные сверла из твердых сплавов марок ВК6М, ВКЮМ.
Спиральное сверло (рис. 0) имеет форму цилиндрического стержня с конусообразным рабочим концом, у которого по сторонам имеются две винтовые канавки с наклоном к продольной оси сверла в 25—30°. По этим канавкам стружка отводится наружу. Угол заточки при
Рекламные предложения на основе ваших интересов:
вершине сверла может быть разным и зависит от обрабатываемого материала. Для обработки мягких материалов он должен быть от 80 до 90°, для стали и чугуна 116—118°, для очень твердых металлов 130—140°.
Заточка сверл. В процессе работы сверла изнашиваются по передней и задней поверхностям, срабатывается фаска, округляются уголки (рис. 1, а). Затупленные сверла затачивают на заточных станках. Контроль основных элементов режущей части осуществляется шаблонами (рис. 1, б).
Рис. 0. Спиральное сверло: 1 — рабочая часть сверла, 2 — шейка, 3 — хвостовик, 4 — лапка, 5 — канавка, 6 — перо, 7 — направляющая фаска (ленточка), 8 — поверхность задней заточки, 9 — режущие кромки, 10 — перемычка, 11 — режущая часть
Ручное сверление осуществляют ручными дрелями, электрическими дрелями и пневмодрелями.
Ручная дрель (рис. 2) состоит из шпинделя, на котором находится патрон, конической зубчатой передачи (состоящей из большого и малого зубчатых колес), неподвижной рукоятки, подвижной рукоятки и нагрудника. Сверло вставляется в патрон и закрепляется в нем. При сверлении слесарь удерживает дрель левой рукой за неподвижную рукоятку, а правой вращает подвижную рукоятку, опираясь грудью на нагрудник.
Рис. 1. Схема износа (а) и шаблон для контроля основных элементов (б) сверла
Электрическая дрель (рис. 3) состоит из электродвигателя, находящегося в корпусе дрели, зубчатой передачи и шпинделя с патроном, в котором зажимается сверло. Различают электрические дрели легкого типа — для сверления отверстий диаметром до 15 мм в форме пистолета; среднего типа — для сверления отверстий диаметром 15—20 мм с замкнутой рукояткой на конце; тяжелого типа — для сверления отверстий диаметром до 32 мм с двумя боковыми рукоятками и грудным упором.
Рис. 2. Ручная дрель: 1 — патрон, 2 — зубчатая передача, 3 — подвижная рукоятка, 4 — нагрудник, б — неподвижная рукоятка
Пневматическая дрель (рис. 4) изготавливается с пневматическими двигателями поршневого и ротационного типа. Пневматическая дрель удобна в работе, так как имеет небольшие габариты и массу. Для механизации процесса сверления используются сверлильные станки.
Рис. 3. Электрическая дрель: 1 — рукоятка, 2 — корпус, 3 — шпиндель
Сверлильные станки подразделяются на настольно- -сверлильные, вертикально-сверлильные и радиально-сверлильные. Настольно-сверлильные станки предназначены для сверления отверстий небольшого диаметра (до 12—15 мм). Радиально-сверлильные
станки применяют для сверления отверстий в крупных деталях. Они дают возможность обработать отверстие в любом месте детали в пределах кольцевой площадки.
Более всего распространены универсальные вертикально-сверлильные станки (рис. 5). Обрабатываемая заготовка или деталь помещается на столе, который можно поднимать и опускать при помощи винта. Рукояткой стол закрепляют на станине на неооходимои высоте. Сверло устанавливают и закрепляют в шпинделе. Шпиндель приводится во вращение электродвигателем через коробку скоростей, автоматическая подача осуществляется коробкой подач. Вертикальное перемещение шпинделя осуществляется вручную маховиком.
Рис. 4. Пневматическая дрель: 1 — шпиндель, 2 — корпус, 3 — ниппель
Техника сверления. Сверление производят по разметке, по кондуктору, с применением универсально-сборных приспособлений (УСП).
При сверлении по разметке размечают отверстие, накернивают его по окружности и по центру, закрепляют обрабатываемую заготовку в тисках или в другом приспособлении. Сверление по разметке обычно осуществляют в два приема. Сначала просзерливают отверстие на глубину четверти диаметра. Если полученное отверстие (несквозное) совпадает с размеченным, то продолжают сверление, в противном случае исправляют установку сверла и только после этого продолжают сверление.
При сверлении отверстия под резьбу необходимо пользоваться справочными пособиями для выбора величины диаметра сверла в соответствии с видом резьбы, а также с учетом механических свойств обрабатываемого материала.
При обработке большого количества одинаковых деталей применяются кондукторы. Они состоят из корпуса, куда укладывается и ориентируется в определенном положении деталь, и кондукторной плиты с отверстиями и запрессованными в них кондукторными втулками для направления сверла.
Кроме кондукторов, применяются универсально-сборные приспособления (УСП), состоящие из нормализованных элементов (плит с Т-образными пазами, установочных деталей — пальцев, дисков, шпонок, подкладок, направляющих, прижимных и крепежных деталей). Из них собирают приспособления для определенной операции. По окончании работы приспособления разбирают, а их детали используют вновь. УСП значительно уменьшают стоимость обработки и обеспечивают высокую точность.
Зенкован и ем называется последующая (после сверления) обработка отверстий, заключающаяся в удалении заусенцев, снятии (фасок и получении конусного или цилиндрического углубления у входной части отверстия. Зенкование осуществляется зенковками.
По форме режущей части зенковки делятся на цилиндрические и конические (рис. 6, а, б). Конические зенковки применяют для обработки конических углублений под головки винтов, потайные заклепки, клапаны. Конические зенковки бывают с углом при вершине 60, 75, 90 и 120°.
Цилиндрическими зенковками обрабатывают цилиндрические углубления под крепежные детали, плоскости бобышек. Цилиндрическая зенковка имеет направляющую цапфу, которая входит в обрабатываемое отверстие и обеспечивает правильное направление зенковки. Зенковки изготавливают из быстрорежущей стали и с пластинками из твердого сплава.
Рис. 5. Одношпиндель-ный вертикально-сверлильный станок: 1 — винт, 2 — стол, 3 — шпиндель, 4 — маховик, 5 — коробка подач, 6 — коробка скоростей, 7 — электродвигатель, 8 — рукоятка, 9 — станина
Зенкерован и е — операция по увеличению размеров или изменению формы отверстия, полученного сверлением, штамповкой или отливкой. При зенкеровании получается точность За — 5-го класса.
Зенкерование отверстий выполняют зенкером. По внешнему виду зенкер напоминает сверло и состоит из тех же основных элементов, но имеет больше режущих кромок (3—4) и спиральных канавок. По конструкции зенкеры разделяют на цельные (рис. 7, а), насадные (рис. 7, б) с напаянными пластинками и сборные со вставными ножами (рис. 7, в). Материалы для зенкеров: быстрорежущие стали Р9, Р18, Р9К5, Р9КЮ, пластинки твердого сплава марок ВК6, ВК8, ВК6М, ВК8В, Т5К10, Т15К6. Зенкерование выполняют на сверлильных станках или при помощи электрических и пневматических дрелей.
Развертывание — окончательная обработка отверстий после сверления, зенкерования или расточки для придания им высокой точности и малой шероховатости. Развертыванием достигается 2—3-й классы точности и классы шероховатости.
Развертывание отверстий выполняется разверткой.
По форме обрабатываемого отверстия развертки подразделяются на цилиндрические и конические, по способу применения — на ручные и машинные, по способу закрепления — на хвостовые и насадные.
Ручные развертки (рис. 58) состоят из рабочей части и хвостовика. Хвостовик цилиндрический с квадратом на конце под вороток. Рабочая часть делится на режущую и калибрующую. Режущая часть имеет коническую форму с углом заборного конуса <р = 1°, на конце для предохранения зубьев от выкрашивания делается фаска под углом 45°.
Чтобы развертка свободно входила в отверстие, диаметр заборной части делают меньше диаметра предварительно обработанного отверстия. Калибрующая часть направляет развертку в отверстие и калибрует его, у заборного конуса она имеет цилиндрическую форму, ближе к хвостовику — обратный конус для уменьшения трения.
Рис. 6. Зенковки:
а — цилиндрическая, б — коническая
Рис. 7. Зенкеры: а — цельный, б — насадной, в — со вставными ножами
Число зубьев развертки четное — 6, 8, 10, 12; выполняют их с неравномерным шагом, что обеспечивает лучшую обработку.
Машинные развертки .отличаются от ручных меньшей длиной рабочей части и длинной шейкой (для развертывания глубоких отверстий). Заборный конус у них короткий с углом ср = 5° для обработки хрупких материалов и ср = 15° для вязких материалов. Развертки, оснащенные твердыми сплавами, имеют угол ф = 35—45°.
Конические развертки служат для обработки предварительно просверленного цилиндрического отверстия на конус или калибрования конического отверстия, выполненного другим способом.
Ручные развертки изготовляют из стали У12А, 9ХС, Р9 и Р18, машинные — из стали Р9, Р18, РК8; они оснащаются твердыми сплавами ВК2, ВК4, ВК6, ВК8, Т15К6. Рабочая часть термически обрабатывается.
Рис. 8. Основные элементы ручной цилиндрической развертки
На развертках наносятся номинальный диаметр (на сборных — предельные диаметры), номер по точности или посадка для доведенной развертки, марки стали или твердого сплава. На конических развертках маркируются номинальный диаметр или номер конуса, конусность, марка стали.
Ручное развертывание. При ручном развертывании инструмент вращается воротками. Для обработки глубоких отверстий на развертку надевают удлинители. Мелкие заготовки или детали закрепляют в тисках, а большие обрабатывают без закрепления.
Машинное развертывание выполняется на сверлильных станках, а также при помощи механизированного инструмента.
Лучше развертывание выполнять сразу после сверления, не перезажимая детали. Это обеспечивает соосность отверстий. При работе на станках применяют качающиеся оправки, они дают возможность развертке самоустанавливаться по оси предварительно обработанного отверстия и исключают влияние неточностей станка на точность отверстия.
Рекламные предложения:
Читать далее: Нарезание резьбы при слесарных работах в автомобилестроении
Категория: — Автомобилестроение
Главная → Справочник → Статьи → Форум
10) Сверление, зенкование, зенкерование, развёртывание отверстий.
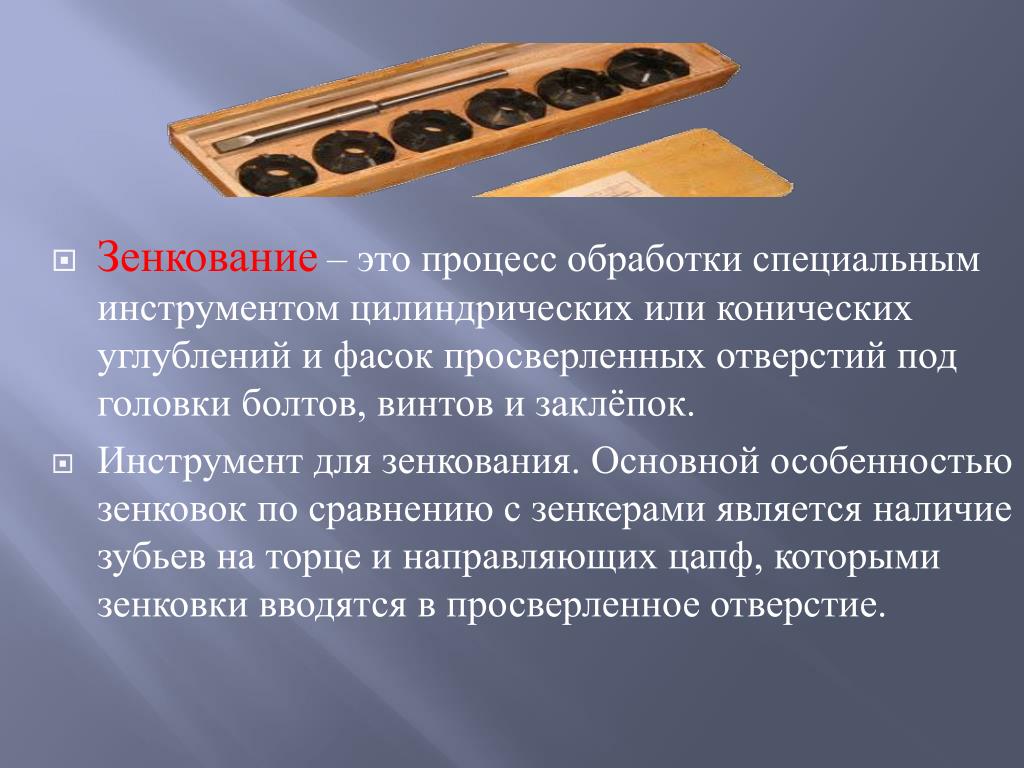
1) Сверлением — называется образование снятием стружки отверстий в сплошном материале с помощью режущего инструмента – сверла. Сверление применяют для получения отверстий не высокой степени точности, и для получения отверстий под нарезание резьбы, зенкирование и развёртывания.
2)
Перовое сверло – данное сверло предназначено для неответственных отверстий диаметром до 25 мм.
Спиральное сверло
Свёрла для глубокого сверления – применяются на специальных станках для получения точных отверстий большей длины малого диметра.
Кольцевое сверло – предназначено для изготовления отверстий в сплошном материале с целью его экономии.
Центровое сверло – предназначено для получения центровых отверстий, применяемых преимущественно в деталях вращения.
Комбинированный инструмент:
Сверло-сверло.
Сверло-зенковка.
Сверло-зенкер.
Сверло-зенкер развёртка.
Сверло-метчик.
3) Ручная дрель — инструмент ручного сверления, при использовании силы человека. Применяется для сверления отверстий в различных материалах.
• Механическое изменение скорости осуществляется изменением передаточного числа редуктора. Обычно используется редуктор с двумя передаточными числами (2-скоростной), реже с бо́льшим. При понижении скорости возрастает крутящий момент, выходная мощность почти не изменяется.
Электрическая
дрель — Дрель
представляет собой инструмент, чаще
всего, в форме пистолета, внутри которого
расположены тяговый преобразователь,
пусковой выключатель, реверс, реостат
или тиристорный регулятор мощности,
электродвигатель (УКД) и (в большинстве
случаев) механизм для сверления с ударом. На валу (шпинделе) дрели расположен
патрон, предназначенный для установки
различных слесарных и строительных
насадок. У мощных дрелей в шпинделе
имеется посадка «конус Морзе» для
непосредственной фиксации в ней сверла.
• Электронная регулировка скорости осуществляется с помощью реостата, который управляется изменением нажатия на кнопку выключателя — чем глубже вдавлена кнопка, тем выше скорость. Часто на кнопке располагается колёсико, которым выставляется ограничение максимальной скорости. При понижении скорости электронным способом выходная мощность снижается. В настоящее время от реостатного управления с большим выделением тепла на реостате перешли к тиристорному управлению мощностью с меньшим выделением тепла.
4) Зенкование – это процесс обработки специальным инструментом цилиндрических или конических углублений и фасок просверленных отверстий под головки болтов, винтов и заклёпок.
5) Зенкерованием — называется процесс обработки зенкерами
цилиндрических и конических необработанных
отверстий в деталях, полученных литьём,
ковкой штамповкой, сверлением, с целью
увеличения их диаметра, качества
поверхности, повышения точности
(уменьшение конусности, овальности).
Зенкеры бывают двух типов:
● Цельные с коническим хвостиком (для предварительной обработки отверстий).
●Насадные ( для окончательной обработки отверстий).
6) Развёртывание – это процесс чистовой обработки отверстий, чем зенкерование и обеспечивающее высокую точность размеров и чистоту поверхности.
7) Развёртки:
По форме обрабатываемых отверстий
Цилиндрические
Конические
По конструкции
Цельные
Насадные
С прямыми и винтовыми зубьями
Постоянные
Регулироваемые
Точность отверстия обработки развёртыванием в соответствии 3-2 классу, а шероховатость поверхности 6-10 класса.
Что такое зенкование — Навыки создателей
Многие люди используют термин зенкование при сверлении пилотных отверстий. Знание того, когда нужно зенковать и как правильно использовать этот метод заворачивания, может быть очень полезным.
Итак, что такое зенковка? Зенкование — это процесс высверливания конической или V-образной области в верхней части пилотного отверстия для головки винта, которое также имеет V-образную форму. Головка винта может располагаться заподлицо или ниже поверхности материала, в котором она просверливается, в зависимости от области применения.
Есть определенные причины, по которым вы захотите использовать зенковку при использовании винтов или болтов. Я объясню эти и некоторые другие советы и приемы ниже, так что продолжайте читать!
Когда использовать зенковку и почему
Основная причина, по которой вы захотите зенковать винт, заключается в том, чтобы головка винта находилась ниже поверхности дерева. Я знаю, о чем вы думаете … Вы можете добиться этого, просто просверлив пилотное отверстие и ввинчивая винт, пока он не войдет под поверхность. Хотя это может быть правдой, часто раскалывается или пузырится вокруг головки винта, оставляя шероховатую поверхность, которую придется немного отшлифовать.
Вы также можете использовать зенковку, чтобы просверлить винт на достаточно большую глубину, на которую вы можете установить красивую деревянную пробку , придавая вашему проекту профессиональный вид. Если вы используете деревянную пробку, убедитесь, что текстура древесины пробки совпадает с направлением вашего проекта.Приятный штрих!
Кроме того, пилотные отверстия и зенковка могут быть очень полезны при работе с любыми видами твердой древесины. Иногда , если древесина достаточно твердая, на самом деле треснет или расколется, если вы попытаетесь вбить в нее шуруп без надлежащего просверливания и зенковки головки винта.
Предварительное сверление и проделывание пилотных отверстий также значительно упрощают сверление шурупом в древесине. Уже одно это снижает вероятность ошибок при сверлении винта.Я много раз пропускал этот важный шаг и часто соскальзываю винт с помощью дрели или сверляю винт под неправильным углом. Я слишком часто учился на собственном горьком опыте, и теперь я почти всегда сверлил пилотное отверстие и зенковал все свои винты.
Что такое растачивание, когда использовать и почему
Зенковка — это процесс высверливания плоской области шириной пилотного отверстия, чтобы было место для крепежа (винта или болта), шайб и торцевого ключа. Отверстие с плоским дном соответствует шайбе и креплению . Если вы утопили отверстие, вместо того, чтобы растачивать его, V-образное отверстие согнет шайбу при затяжке винта или болта.
Аналогично зенковке, если вы расточите крепежную деталь достаточно глубоко, вы также можете использовать пробку для заполнения материала. Следует учитывать, понадобится ли вам доступ к застежке; скажем болт. Вам не нужно растачивать болт и закрывать его заглушкой, если вам по какой-либо причине придется разбирать болт .
Вытащить заглушки из материалов может быть непросто и отнимать много времени. Подумайте заранее, прежде чем решать, насколько глубоко растачивать отверстие.
Различные типы сверл с зенковкой
Существует множество различных типов сверл, которые можно использовать для зенковки винтов. При выборе сверла с зенковкой также необходимо убедиться, что угол наклона сверла соответствует типу винта или крепежа, который вы собираетесь использовать.Если он не совмещен должным образом, вы действительно немного потеряете прочность соединения между винтом и материалом.
Наиболее распространенные углы винта в США составляют 82 ° и 90 °. Другие степени зенковки — 60 °, 100 °, 110 ° и 120 °. Если вы зенковываете металл или твердую древесину, угол наклона более важен, чем если бы вы просто сверлили мягкую древесину, потому что головка винта не войдет должным образом в потайное отверстие.
Вот список наиболее распространенных сверл с зенковкой.
- Комбинация зенковки и сверла — я начну с этого, потому что это то, что я использую большую часть времени. Комбинированное сверло — это именно то, что вы думаете… два сверла в одном! Часть сверла с зенковкой создает V-образный вырез для головки винта, а фактическая часть сверла просверливает пилотное отверстие. Наличие обоих сверл в одном экономит время, потому что вам не нужно сверлить пилотное отверстие, менять зенковку, просверливать отверстие и снова переключаться на сверло для пилотного отверстия.
- Насадка с зенковкой с одной канавкой — Эта насадка с зенковкой имеет одну режущую кромку и одну канавку для удаления отходов. Вы все равно захотите сначала просверлить пилотное отверстие обычным сверлом.
- Сверло с зенковкой с несколькими зубьями — Сверло с зенковкой с несколькими канавками. Дополнительные канавки по сравнению с фрезой с зенковкой с одной канавкой делают ее более эффективной при резке и удалении отходов.
Опять же, как и в случае с коронкой с одной канавкой, вам нужно просверлить пилотное отверстие.
- Комбинация зенковки и удаления заусенцев с нулевой канавкой — Эта коронка обычно используется для обработки металла, а функция удаления заусенцев помогает удалить острые заусенцы, оставшиеся после сверления отверстия. Обязательно используйте его после того, как в металле просверлите пилотное отверстие.
- Насадка для установки шурупов для гипсокартона — Используется для ввинчивания шурупов для гипсокартона на нужную глубину, обеспечивая идеальную зенковку. Я расскажу подробнее ниже.
Кроме того, если вы хотите заполучить коронку для зенковки и планируете использовать деревянные заглушки, чтобы прикрыть винты с потайной головкой, есть отличные комбинированные наборы , в которых есть зенковки вместе с коронками для заглушек подходящего размера .Обязательно ищите их во время покупок, чтобы облегчить себе жизнь!
Как установить глубину зенковки
Получение одинаковой глубины отверстий с потайной головкой может оказаться непростой задачей, если у вас нет доступа к сверлильному станку. Сверлильные станки обычно имеют удобный ограничитель глубины сбоку, что позволяет вам всегда идеально сверлить.
Если вы используете стандартную ручную дрель, установка идеальной глубины зенкования может быть такой же простой, как и на сверлильном станке, если вы знаете правильный трюк… Обычные способы установки глубины зенкования имеют недостатки.Распространенные способы установки глубины и их недостатки:
Method | Downside |
Маркировка сверла маркером | Вы должны оставить постоянную отметку на сверле. Придется попробовать и увидеть, как он вращается с невероятно высокой скоростью через опилки или металл. |
Маркировка сверла лентой | Я не хочу, чтобы клейкая лента на моем сверле. Лента скользит вверх при интенсивном использовании и снижает точность. |
Использование стоп-воротник на вашем буровое долото | Они вращаются с буровым долотом, оставляя следы на поверхности материала.![]() |
К счастью, вы можете легко сделать упор глубины из обрезков древесины , чтобы каждый раз точно настраивать глубину зенкования. Просто следуйте этим простым шагам.
- Найдите небольшой кусок древесины для зенковки.
- Просверлите отверстие размером с хвостовик сверла (без зенковки) через блок.
- Просверлите второе отверстие посередине деревянного бруска, размер которого соответствует размеру вашей зенковки.
- Проверьте глубину зенковки и при необходимости подрежьте деревянный брусок, пока не получите желаемую толщину.
Квадратная или прямоугольная форма вашего блока позволяет легко удерживать его, поэтому он не вращается и не оставляет следов на вашем материале.
Как зенковать шурупы для гипсокартона
При навешивании гипсокартона вам нужно зенковать винты чуть ниже бумажной части гипсокартона.Если вы не просверлите винт достаточно глубоко, вам будет непросто замутить винт, потому что вам придется добавить много гипсокартона в окружающую область.
Затем вам нужно отшлифовать и растушевать большую неровность, которую вы только что создали, чтобы сделать ее не такой заметной. Это любительская ошибка , которая убивает производительность, эффективность и, что хуже всего, заставляет ваш гипсокартон плохо выглядеть.
Грязь для гипсокартона намного проще, когда все винты утоплены и расположены чуть ниже поверхности.Вы поймете, когда это будет сделано правильно, потому что будет ощущаться плотно, а не проталкивать сквозь бумагу и продолжать движение.
Если вы вешаете много гипсокартона, вы можете подумать о приобретении специальной отвертки для гипсокартона . По сути, это сверла с буртиком на внешней стороне насадки для отвертки. Он ударяется о гипсокартон в определенной точке (которую вы можете отрегулировать по своему вкусу) и не дает вам слишком сильно ввинтить шуруп. Они работают очень хорошо, и я настоятельно рекомендую их проверить, потому что они созданы специально для точного зенкования шурупов для гипсокартона и отлично справляются со своей задачей.
Способ бедняка зенковать шурупы для гипсокартона — это использовать стандартную электрическую отвертку и заворачивать шуруп так, чтобы головка шурупа едва касалась гипсокартона. Затем вы хотите немного повернуть винт, используя крошечные приращения, чтобы он располагался чуть ниже бумаги, а не слишком глубоко там, где он не будет удерживать гипсокартон должным образом.
Существует также несколько различных типов установочных битов для гипсокартона , которые вы можете использовать вместо стандартной отвертки в вашем сверле.Они работают довольно хорошо и стоят довольно дешево. Если вы хотите купить один из них, у меня есть два совета.
- Совет № 1 — Убедитесь, что у вас нет слишком широкой биты для установки шурупов. Если у вас слишком широкое сверло, будет сложно зенковать шурупы на стыках гипсокартона, где вам придется сверлить под углом.
- Совет № 2 — Ищите намагниченные биты для установки шурупов для гипсокартона.
Отличное крепление винта к сверлу — полезная функция, которая упрощает работу и экономит время.
Зенковка металла
Прежде всего, убедитесь, что вам нужно использовать зенкерную коронку, а не зенковку, прежде чем начинать сверление в вашем проекте. Если вы только что перешли к этому разделу, я объясню больше в разделе о растачивании выше, так что проверьте его, если вы еще этого не сделали.
Для зенковки крепежа в металл я предпочитаю использовать трехэтапный процесс. Последний шаг не обязателен. Мне также нравится использовать какой-нибудь тип масла для уменьшения нагрева и трения между металлом и сверлом.Tap Magic Cutting Fluid — это особый тип, который я использую, но если у меня закончится, я просто воспользуюсь WD-40.
- Сначала я пробурил фактическую пилотную скважину с помощью сверла из черной оксидной или кобальтовой стали. Однако обычно подойдет любое сверло из быстрорежущей стали (HSS).
HSS имеет тенденцию тускнеть и изнашиваться намного быстрее на металле, потому что он не такой мягкий, как дерево. Я буду время от времени останавливаться и добавлять немного масла.
- Затем я переключу биты на зенковку и комбинированное сверло для удаления заусенцев, добавлю немного больше масла на поверхность вокруг отверстия, и просверлил мое отверстие с зенковкой до нужной глубины .Я люблю дважды проверять глубину, вставляя винт или фиксатор в отверстие с потайной головкой и убедившись, что он находится там, где мне нужно.
- Третий шаг не обязателен. Если пилотное отверстие в металле проходит через весь кусок металла, мне нравится перевернуть металл и слегка зенковать и удалить заусенцы с другой стороны . Это помогает удалить все, что осталось от сверления первого отверстия в металле.
Вывод зенковки
Зенковка очень проста в выполнении и действительно улучшает внешний вид ваших проектов.Надеюсь, я ответил на все ваши вопросы о зенковании, а также о любой другой проблеме, которая могла возникнуть у вас в голове во время чтения. Если нет, спросите в разделе комментариев ниже… Я здесь, чтобы помочь!
Proto Tech Tip: зенковка — Protocase Blog
Каждую неделю Team Protocase представляет вам видеоролик Proto Tech Tip, в котором мы даем информативный взгляд на отдельные аспекты производства листового металла и обработки с ЧПУ.
На этой неделе Allison кратко расскажет о зенковке для винтов с плоской головкой и о том, почему они являются полезным дополнением к индивидуальному корпусу или детали.
Посмотрите полное видео ниже — или, если вы предпочитаете прочитать его Proto Tech Tip, у нас есть полная расшифровка под видео.
Обязательно подпишитесь на канал Protocase на YouTube, чтобы не пропустить ни одного Proto Tech Tip!
Всем привет, Эллисон здесь из Protocase с еще одним советом Proto Tech. Сегодня речь идет о зенковке.
Таким образом, крепежные винты бывают с полукруглой или плоской головкой. Чтобы установить винт с плоской головкой, вырез, в который он устанавливается, должен быть потайным.
Зенкование — это использование сверлильного станка для создания в детали конического отверстия, соответствующего углу и размеру головки конкретного винта.
Зенковка гарантирует, что винты будут плотно прилегать к металлической поверхности корпуса или детали. Итак, есть три основные причины, по которым обычно используется зенковка. Первое — избегать помех. Например, в полноразмерном корпусе для монтажа в стойку, если вы используете винты с полукруглой головкой, корпус, скорее всего, будет тереться о корпус, установленный сверху или снизу.Винты с потайной головкой с потайной головкой создадут ровную поверхность, что даст вам больший зазор.
Еще одна причина, по которой некоторые дизайнеры предпочитают использовать зенковки, заключается в том, что им нужно создать хорошее уплотнение. Например, вам может потребоваться светонепроницаемый корпус. Конечно, в этом случае пригодятся и прокладки.
Наконец, зенковка также отлично подходит для создания обтекаемого вида. Многие дизайнеры из-за эстетики отдают предпочтение винтам с потайной головкой.
Итак, есть несколько требований к конструкции, которые необходимо учитывать при выборе зенковки. Во-первых, вы должны заранее сообщить нам, какой тип винта вы хотите использовать. Каждому винту
соответствует размер резьбы. Размер резьбы также указывает угол зенковки на головке. Так, например, размер резьбы 100 градусов номер 2 означает угол зенковки 100 градусов при стандартном размере резьбы 2-56.
Итак, еще один совет: материал утопленной детали также должен быть достаточно толстым, чтобы выдержать глубину головки используемого винта.Если ваш материал недостаточно толстый, ваш винт выйдет на дно, прежде чем он окажется на одном уровне с поверхностью. Стандартные винты обычно имеют угол наклона 100, 90 или 82 градуса. Если вы хотите использовать крепеж, которого нет на складе Protocase, а внешний диаметр головки винта больше, чем обычно, просто свяжитесь с нами. Скорее всего, мы сможем настроить сверлильный станок по индивидуальному заказу, чтобы подобрать то, что вы ищете.
Зенковка обычно выполняется перед нанесением порошкового покрытия на деталь.Итак, как вы можете видеть на образце, у нас есть несколько стандартных зенковок. Сверху у нас есть зенковки с черным порошковым покрытием Sandtex, а внизу — зенковки с зернистой отделкой.
Таким образом, обычно вы всегда должны учитывать номинальную толщину, которую порошковое покрытие добавит к вашему вырезу, чтобы гарантировать, что застежка будет правильно помещаться в вырез. Но при зенковании вам фактически не нужно учитывать дополнительную толщину порошкового покрытия, потому что наши зенковки достаточно глубоки, чтобы учесть эту дополнительную толщину
.
Итак, совет: Protocase Designer — это наше программное обеспечение для 3D-дизайна, которое позволяет создавать потайные вырезы прямо в вашем дизайне. Мы связались с руководством по этому поводу ниже. Звоните
, чтобы получить дополнительную информацию на нашем веб-сайте.
В приведенном ниже описании мы помещаем несколько прямых ссылок на наши многочисленные варианты застежек, которые мы предлагаем. Не забудьте также заглянуть в наш блог, в котором содержится множество других технических советов.
просто отправьте нам письмо по адресу info @ protocase.com.
Большое спасибо за просмотр Proto Tech Tip на этой неделе. Удачного проектирования! Увидимся на следующей неделе
Винты с зенковкой и плоской головкой
Зенковка
Protocase Tech Tip Видео
Краткое видео о зенковке
При зенковке используется сверлильный станок для создания конического отверстия в части или корпусе, которое соответствует углу и размеру головки конкретного винта с плоской головкой.
Зенковка идеально подходит для обеспечения того, чтобы винты с плоской головкой прилегали заподлицо с металлом вашего индивидуального корпуса или детали.
Щелкните здесь, чтобы просмотреть нашу подборку винтов с плоской головкой.
Преимущества зенковки
Расположение винтов с плоской головкой заподлицо с металлом детали или корпуса может быть выгодным по нескольким причинам:
Предотвращение помех: это особенно важно для полноразмерных стоечных шкафов.Обеспечивая надлежащий зазор между корпусами, вы избежите их трения о корпус, установленный сверху или снизу.
Создание хорошего уплотнения: помимо использования специальных прокладок, использование винтов с потайной головкой может помочь в создании светонепроницаемого или пыленепроницаемого корпуса.
Достижение обтекаемого вида: многие дизайнеры предпочитают винты с потайной головкой из-за эстетики гладкой поверхности.
Стандартные размеры зенковки
Protocase предлагает стандартные углы зенковки 82, 90 и 100 градусов.
Если вам требуется нестандартный угол зенковки, свяжитесь с нами, чтобы обсудить ваши варианты.
Ограничения
Зенкование доступно для всего нашего листового металла.
Материал утопленной детали должен быть достаточно толстым, чтобы соответствовать глубине головки используемого винта. Если материал недостаточно толстый, ваш винт выйдет из строя до того, как он окажется на одном уровне с поверхностью.
Чтобы винт с плоской головкой прилегал заподлицо, толщина материала панели должна быть как минимум такой же высоты, как и глубина головки винта.
Если вам нужна помощь в выборе толщины металла, соответствующей вашим винтам и зенковке, свяжитесь с нами.
Конструктор Протокейсов
Выбор зенковки в Protocase Designer, нашем бесплатном программном обеспечении для проектирования корпусов, — это быстрый и простой процесс. Щелкните здесь, чтобы посмотреть руководство.
Архивы зенковки — Harvey Performance Company
Станок с двухугольным хвостовиком часто называют «швейцарским армейским ножом для механической обработки» из-за его исключительной универсальности. Этот уникальный инструмент можно использовать для снятия фасок, снятия обратной фаски, фрезерования V-образных канавок, снятия заусенцев и зенкования. Ниже мы узнаем нюансы каждой операции и узнаем, почему фрезы с двойным угловым хвостовиком могут быть отличным инструментом, который всегда под рукой в любой механической мастерской.
1. Фрезерование резьбы
Как по назначению, так и по внешнему виду, фрезы с двойным угловым хвостовиком очень похожи на фрезы для одинарной резьбы. Фрезы для одинарной резьбы более универсальны, чем фрезы для множественной резьбы, поскольку они не имеют фиксированного шага.Двухугловые фрезы с хвостовиком и углом 60 ° могут создавать внутреннюю и внешнюю 60 ° унифицированную национальную (UN) и метрическую резьбу. Двухугловые фрезы с хвостовиком под углом 55 ° можно использовать для нарезания трубной резьбы 55 ° по британскому стандарту (BSPT). Чтобы определить размеры резьбы, которые могут производить различные фрезы с двойным угловым хвостовиком, полезно обратиться к таблицам посадки резьбы, в которых соответствующие диаметры фрезы сочетаются с требуемым размером резьбы.
2. Снятие фаски
В зависимости от требований операции снятия фаски и угла фаски, которую вы создаете на вашей детали, может подойти фреза с двухугольным хвостовиком.Угол верхней или нижней кромки режущей поверхности инструмента (обозначенный ниже как размер B1) будет определять угол фаски вашей детали. Область, отмеченная красным на рисунках 2 и 3 ниже, обозначает участок резки для операции снятия фаски и обратной фаски (оставляя фаску на нижней части детали).
Для получения дополнительной информации об углах двухугловых фрез с хвостовиком см. Полезное руководство Harvey Tool: «Углы без углов».
3.Снятие задней фаски
Рассмотрим сквозное отверстие, в котором есть заусенец или надрыв в результате сверления задней части заготовки. Изменение ориентации заготовки и перемещения отверстия занимает много времени, и может быть трудно точно закончить отверстие. В таком случае предпочтительным методом является снятие задней фаски с просверленного отверстия без изменения настройки. Проще говоря, возможность точно снимать фаски не только с верхней, но и с нижней стороны детали без необходимости повторного закрепления заготовки на станке, что сэкономит драгоценное время и деньги.
Для получения наилучших результатов при снятии фасок с помощью двухугольных фрез с хвостовиком используйте технику перешагивания с уменьшением проходов по мере увеличения радиального зацепления. Эта стратегия помогает управлять степенью контакта по углу и может значительно избежать отклонения инструмента.
4. Обработка V-образных канавок
Двухугловая фреза с хвостовиком обычно применяется для обработки профилей с V-образной канавкой, так как ее режущая головка расположена перпендикулярно центральной линии инструмента.Это обеспечивает эффективное резание даже при низкой скорости шпинделя. Низкая скорость острия может привести к проблемам с другими инструментами, такими как фрезы для снятия фаски, где заостренный профиль находится по центру инструмента.
5. Удаление заусенцев
Работа по удалению заусенцев с деталей может быть утомительной для вас и неэффективной для вашего цеха. Это также может привести к неточностям в деталях, требующих точных размеров. Фрезы с двухугольным хвостовиком можно использовать для удаления заусенцев прямо на вашем станке с ЧПУ.Благодаря этому процесс отделки детали становится простым, быстрым и точным. Конечно, очень важно обеспечить надлежащий зазор перед обработкой дна обработанного отверстия.
Другие полезные и универсальные инструменты для быстрого удаления заусенцев с ЧПУ включают концевые фрезы для удаления заусенцев, фрезы для удаления заусенцев с обратной стороны, концевые фрезы для подрезки и фрезы для снятия фасок.
6. Зенковка
Зенковка детали выполняется таким образом, чтобы винт, гвоздь или болт мог прилегать заподлицо с поверхностью детали.Использование специальных профильных инструментов может помочь увеличить край просверленного отверстия и скосить стороны, чтобы винт точно сидел. Фрезы с двойным угловым хвостовиком также могут выполнять эту операцию, используя нижнюю часть своей режущей поверхности.
Благодаря своей способности выполнять шесть различных операций, фрезы с двойным угловым хвостовиком являются идеальным инструментом для использования в карусели инструментов. В связке эти инструментальные формы могут выполнять фрезерование резьбы, фаски, задней фаски, обработки V-образных канавок, удаления заусенцев на вашем станке с ЧПУ и зенковки.Эта универсальность делает его фаворитом в области обработки и может предложить цехам повышенную производительность за счет устранения необходимости переворачивать детали, снимать заусенцы вручную или носить с собой различные формы инструментов.
Для получения дополнительной информации о фрезах с двойным угловым хвостовиком Harvey Tool щелкните здесь.
Зенковка авиационных материалов | Производство режущего инструмента
Все более широкое использование титана и абразивных композитов в авиационной промышленности привело к разработке зенковки нового поколения.![]() |
Основное умение авиастроителей — это способность скреплять два куска материала вместе таким образом, чтобы они не разлетались на части со скоростью 3 Маха при повороте на 90 °. Это требует точной подготовки отверстия перед установкой крепежа, в частности зенковки.
В конце 30-х годов прошлого века была разработана клетка с микростопором. Зенковка с резьбовым хвостовиком ввинчивается в устройство, которое приводится в движение ручным электродвигателем дрели и позволяет механику регулировать глубину зенковки на 0.001 «с хорошей точностью и воспроизводимостью. Базовая конструкция микростопов не претерпела существенных изменений за последние 60 лет. Однако современные микростопы намного прочнее и точнее, они включают улучшенную технологию подшипников для достижения требуемых более высоких скоростей вращения. для современных экзотических материалов (рис. 1).
Производители самолетов заинтересованы в улучшенных версиях этих инструментов с ручным управлением, несмотря на автоматизацию их процессов. Автоматическое крепление становится все более распространенным, поскольку машины разрабатываются с возможностью обработки больших панелей.Например, крыло можно собрать на очень большой машине Gem-Cor, большом приспособлении, на котором устанавливается крыло. Предварительно запрограммированный робот просверливает и зенковывает отверстие за одну операцию с помощью комбинированного сверла / зенковки (робот также вставляет крепежный элемент и при необходимости сбривает его головку).
Тем не менее, подавляющее большинство зенковки отверстий по-прежнему выполняется в отдельной операции с использованием ручных сепараторов с микростопорами, потому что создание машины, достаточно большой для обработки больших деталей самолета, в большинстве случаев нецелесообразно.
Рис. 1: Блок клетки для микростопа, используемый для ручных операций зенковки. |
Новые материалы, новые инструменты
В прошлом самолеты конструировались в основном из алюминия. Зенковки из быстрорежущей стали с 2 или 3 зубьями были отраслевым стандартом. С появлением титана и других твердых и абразивных материалов твердосплавные инструменты с 2 и 3 зубьями начали проникать в промышленность.Современные композитные материалы еще более абразивны и требуют использования режущих кромок из поликристаллического алмаза (PCD).
Резьбовые зенковки поставляются со съемными или встроенными направляющими. Преобладает стиль интегрального пилота (рис. 2), так как он имеет контролируемый радиус скругления на пересечении угла и пилота, что обычно используется в авиационной промышленности для зенковки. Эта конструкция устраняет острый угол, который является точкой напряжения на инструменте. Радиус шлифуется одновременно с шлифовкой пилота для обеспечения касания.
В большинстве случаев, если такой радиус был заточен в съемный пилотный инструмент, пользователь мог использовать пилот только одного размера для этого инструмента. Это устраняет главное преимущество съемного пилота — возможность использования множества разных пил, так что не требуется отдельная зенковка для каждого размера отверстия. И если пилот не выровнялся правильно из-за биения отверстия или хвостовика пилота, пользователь может забить отверстие или получить частичный радиус в заготовке.
Рисунок 2: Твердосплавная зенковка со встроенным пилотным элементом. |
Твердосплавная версия интегрально-пилотного инструмента изготавливается двумя способами: с твердосплавными напайками, в которых режущие кромки твердосплавные, а пилотный — HSS; или твердый сплав, у которого вся передняя часть инструмента выполнена из твердого сплава. Инструмент с твердосплавными напайками дешевле, но имеет меньший срок службы, чем цельный инструмент, из-за износа пилота из быстрорежущей стали. Чем более абразивным является материал заготовки, тем короче срок службы инструмента. Инструмент из твердого сплава лучше, если рассматривать стоимость отверстия, а не стоимость инструмента.
Обработка композитов
Увеличение использования композитных материалов в авиастроении изменило тип и конфигурацию зенковок, используемых сегодня. Основное изменение заключается в более высоких степенях зазора — от 16 ° до 20 ° в основном на инструменте PCD по сравнению с 6 ° до 10 ° на твердосплавном инструменте для титана или от 3 ° до 4 ° на инструменте из быстрорежущей стали для стали. Инструменты, предназначенные для резки Kevlar®, дополнительно имеют широкую зубчатую канавку в сочетании с большим свободным углом.
Для композитов оптимальным инструментальным материалом является PCD. При работе с композитными материалами HSS обычно вообще не работает из-за сильно ускоренного износа инструмента. Карбид будет работать, но со значительно меньшим сроком службы инструмента по сравнению с титаном. Тем не менее, иногда необходимо использовать твердый сплав, а не PCD, когда определенная геометрия, требуемая на режущем инструменте, не может быть достигнута с помощью заготовок из PCD — например, острие сверла или радикально зацепленная поверхность для зенковки из кевлара без заусенцев.См. Таблицу 1, где указаны рекомендуемые материалы режущего инструмента для различных материалов заготовки.
PCD нельзя использовать в черных металлах. Поскольку он основан на углероде, при нагревании он становится единым целым с заготовкой. Таким образом, он ограничен применениями из цветных металлов и композитов. Для обработки черных металлов требуются инструменты из карбида или быстрорежущей стали.
| ||||||||||||||||||||||||||||||||
Таблица 1: Рекомендации по инструментальным материалам для различных материалов самолетов. |
Не следует наносить СОЖ при зенковке композитов с помощью инструментов PCD. Охлаждающая жидкость имеет тенденцию вступать в реакцию с композитом и вызывать расслоение. И в этом нет особой необходимости, потому что PCD имеет очень хорошие характеристики теплопередачи. При использовании карбида на композитах может помочь спрей холодного воздуха.
Рисунок 3: Зенковка с закругленной кромкой PCD со сменными лезвиями и направляющими. |
PCD формирует вверх
Одна из проблем, с которыми сталкиваются мастерские при работе с PCD, — это ограниченная возможность шлифования инструментов определенной геометрии. Но компания Craig Tools Inc., Эль-Сегундо, Калифорния, разработала инструмент для решения этой проблемы — Versi-Sink, зенковку со сменным лезвием, съемным пилотом и резьбовым хвостовиком (рис. 3). В отличие от других зенковок PCD, инструмент со сменным лезвием имеет контролируемый радиус скругления. Обычно такой радиус скругления трудно достичь на зенковке PCD, особенно в конфигурации с двумя канавками, без изменения высоты кромки.Крейг добился этого, шлифуя лезвия отдельно на специально приспособленном для этого приспособлении, а затем механически удерживая лезвия в корпусе. Versi-Sink принимает сменные ножи с контролируемым радиусом или сменные прямые ножи для использования, когда радиус не требуется. Инструмент может использоваться в конфигурации с 1 или 2 зубьями. Пилот также можно заменить, так что по мере его износа или изменения размера обрабатываемого отверстия можно установить новый пилот и использовать тот же набор лопастей.Радиус будет оставаться касательным к диаметру пилота, поскольку пластина расположена на шлифованной плоскости на хвостовике пилота, и может быть установлен механиком без использования оптического компаратора. Это обеспечивает большую универсальность, чем традиционная зенковка со съемной направляющей.
Если радиус скругления не требуется, можно использовать зенковку из PCD с двумя канавками и без радиуса (Рисунок 4). Конструкция с 2 зубьями обычно предпочтительнее конструкции с 1 или 3 зубцами. Баланс и режущее действие превосходны, пока инструмент имеет хорошую высоту кромки.Если одна канавка выступает слишком сильно, это приведет к вибрации и отверстиям в форме яйца. В прошлом эта проблема была более распространенной, поэтому пользователи выбрали зенковки из PCD с 1 канавкой, чтобы избежать этой проблемы и минимизировать стоимость алмазов.
Рисунок 4: Зенковка PCD без радиации со сменными лезвиями и направляющими. |
Паяная зенковка из PCD с 2 зубьями легко ремонтируется при условии, что у пользователя есть подходящее оборудование.Эти инструменты, как и все инструменты PCD, имеют очень большие задние углы, которые необходимо поддерживать при переточке инструмента, чтобы предотвратить резкое снижение производительности. Эта проблема часто возникает, когда пользователь пытается самостоятельно обслуживать эти инструменты. PCD чрезвычайно трудно шлифовать на стандартном инструментально-шлифовальном станке. Пытаясь просто очистить режущую кромку, оператор может уменьшить величину зазора, удалив меньше материала, чтобы облегчить работу. Такой подход эффективно уменьшает зазор на режущей кромке.Поэтому, как правило, гораздо экономичнее отправить инструмент обратно производителю для ремонта.
Стоимость отверстия
Ниже приводится сравнение затрат на отверстие для ламината из графита и эпоксидной смолы:
Фреза из быстрорежущей стали | от 30 до 50 отверстий |
Фреза с твердосплавными напайками | От 300 до 500 отверстий |
Фреза с полукруглой кромкой и радиусом скругления | от 5000 до 10000 отверстий |
Резак из быстрорежущей стали по 5 долларов за штуку, без переточки | 5 долларов США / 50 отверстий = 0 долларов США.![]() |
Твердосплавный резак по 28 долларов за штуку, две переточки по 8,35 долларов за каждую, стоимость ремонта 16,70 долларов | 44,70 $ / 1500 отверстий = 0,03 USD / отверстие |
Фреза с пластинами PCD с радиусом скругления по 39,45 долларов США каждая, 10 пилотов по 19,85 долларов США или 198,50 долларов США, набор пластин по 220,75 долларов США каждая, три переточки по 83,75 долларов США или 251,25 долларов США на восстановление. | 709,95 USD / 40 000 отверстий = 0,0177 USD / отверстие |
Зенковка из быстрорежущей стали, интегральная пилотная, с резьбовым хвостовиком, вероятно, никогда не будет полностью выведена из употребления, но существует определенная тенденция к увеличению количества инструментов из твердых сплавов и поликристаллических алмазов.Эффект от использования PCD постепенно исчезает по мере того, как все более широко признается экономия затрат на отверстие. Многие компании заметили, что их затраты на скоропортящийся инструмент резко выросли, поскольку они покупают все больше и больше твердосплавных инструментов для удовлетворения потребностей своих мастерских и получают все меньше и меньше отверстий на инструмент из-за более широкого применения композитных материалов. Тогда инструмент PCD становится намного более привлекательным как средство снижения затрат и повышения производительности за счет значительного сокращения смены инструмента и радикально большего количества отверстий на инструмент.
Промышленность режущего инструмента может рассчитывать на расширение использования композитов во всех областях производства. В авиационной промышленности это означает постоянный переход к инструментам из твердых сплавов, поликристаллических алмазов и инструментов с покрытием. Стоимость отверстия всегда будет решающим фактором при выборе режущего инструмента.
Об авторе
Уильям Кливленд — президент Craig Tools Inc. , Эль-Сегундо, Калифорния. Он также является президентом Института режущего инструмента США в Кливленде.
зенковка — определение и значение
Сверла должны быть приобретены у различных дилеров, но могут быть изготовлены из стальной проволоки, размягченной в огне и опиленной до острого треугольника, а затем закаленной до твердости для яиц меньшего размера, или опилки для больших яиц. яйца по выкройке « зенковка » по дереву; действительно, самый маленький
Практическая таксидермия Пособие для любителя по сбору, сохранению и настройке естествознания всех видов.К этому добавлена глава о художественном оформлении музеев. С дополнительными инструкциями по лепке и художественной таксидермии.
В качестве альтернативы, они могут быть дооснащены такими устройствами, как зенковка , калибр , в ситуациях, когда обычные индикаторы с соотношением 1: 1 будут бесполезны.
Manufacturingtalk — новости обрабатывающей промышленности
В качестве альтернативы, они могут быть дооснащены такими устройствами, как зенковка , калибр , в ситуациях, когда обычные индикаторы с соотношением 1: 1 будут бесполезны.
Manufacturingtalk — новости обрабатывающей промышленности
В качестве альтернативы, они могут быть дооснащены такими устройствами, как зенковка , калибр , в ситуациях, когда обычные индикаторы с соотношением 1: 1 будут бесполезны.
Manufacturingtalk — новости обрабатывающей промышленности
В качестве альтернативы, они могут быть дооснащены такими устройствами, как зенковка , калибр , в ситуациях, когда обычные индикаторы с соотношением 1: 1 будут бесполезны.
Manufacturingtalk — новости обрабатывающей промышленности
В качестве альтернативы, они могут быть дооснащены такими устройствами, как зенковка , калибр , в ситуациях, когда обычные индикаторы с соотношением 1: 1 будут бесполезны.
Manufacturingtalk — новости обрабатывающей промышленности
В качестве альтернативы, они могут быть дооснащены такими устройствами, как зенковка , калибр , в ситуациях, когда обычные индикаторы с соотношением 1: 1 будут бесполезны.
Manufacturingtalk — новости обрабатывающей промышленности
В качестве альтернативы, они могут быть дооснащены такими устройствами, как зенковка , калибр , в ситуациях, когда обычные индикаторы с соотношением 1: 1 будут бесполезны.
Manufacturingtalk — новости обрабатывающей промышленности
В качестве альтернативы, они могут быть дооснащены такими устройствами, как зенковка , калибр , в ситуациях, когда обычные индикаторы с соотношением 1: 1 будут бесполезны.
Manufacturingtalk — новости обрабатывающей промышленности
В качестве альтернативы, они могут быть дооснащены такими устройствами, как зенковка , калибр , в ситуациях, когда обычные индикаторы с соотношением 1: 1 будут бесполезны.
Manufacturingtalk — новости обрабатывающей промышленности
Зенковка, зенковка и точечная наплавка — 2: Зенковка | ||||||||||||||||||
ПРЕДУПРЕЖДЕНИЕ : Станки представляют угрозу безопасности.![]() | ||||||||||||||||||
Зенковка — это операция создания поверхности конической или конической формы на входе в отверстие с целью размещения головки винта с плоской головкой, авиационной заклепки или другого аналогичного крепежа заподлицо или ниже поверхности.Эта форма конуса обрабатывается зенковкой. | ||||||||||||||||||
Зенковки доступны как с одной, так и с несколькими зубьями.![]() | ||||||||||||||||||
Указатели для снятия фаски могут использоваться для точного контроля глубины фаски | ||||||||||||||||||
Зенковка 90 ° обычно используется для удаления заусенцев или острых краев отверстий.![]() Инструменты для зенковки бывают разных размеров (внизу слева) и даже специальной формы, например, инструменты для зенкования (внизу справа) | ||||||||||||||||||
Большинство головок винтов с плоской головкой имеют угол наклона 80/82 ° или 100 °.Поэтому некоторые механики называют эти инструменты для зенковки, а углы 30 °, 45 °, 60 ° и 90 ° — инструментами для снятия фаски. Р.С. | ||||||||||||||||||
этикетка: зенковка, зенковка, точечная обработка | ||||||||||||||||||
