Зенковка — Википедия
Материал из Википедии — свободной энциклопедии
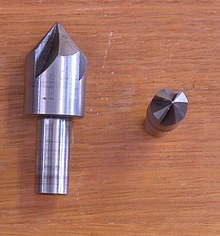
Зенко́вка — многолезвийный режущий инструмент для обработки отверстий в деталях с целью получения конических или цилиндрических углублений, опорных плоскостей вокруг отверстий или снятия фасок центровых отверстий. Применяется для обработки просверлённых отверстий под головки болтов, винтов и заклёпок.
Зенковки для цилиндрических углублений и опорных плоскостей часто называют цековками.
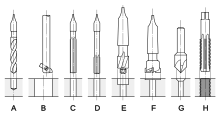
По форме режущей части зенковки подразделяются на:
- цилиндрические
- конические
- торцовые (цековки).
Цилиндрические зенковки состоят из рабочей части и хвостовика. Для обеспечения соосности отверстия и образованного зенковкой углубления имеют направляющую цапфу.
Конические зенковки также состоят из рабочей части и хвостовика. Для обеспечения соосности отверстия и образованного зенковкой углубления могут иметь направляющую цапфу. Бывают прямые и обратные-двухсоставные (используемые при отсутствии прямого подхода).
Цековки предназначены для зачистки торцевых поверхностей бобышек под шайбы, упорные кольца или гайки.
По диаметру обрабатываемых отверстий:
- для отверстий от 0,5 до 1,5 мм (простые)
- для отверстий от 0,5 до 6 мм (без предохранительного или с предохранительным конусом)
- для отверстий от 8 до 12 мм (с конусным хвостовиком)
- ГОСТ 14953—80 Зенковки конические. Технические условия
Зенковка — что это, виды и применение, конструкция, зенкование и ГОСТ.
Зенковка – это металлорежущий инструмент с несколькими рабочими лезвиями, предназначенный для обработки предварительно просверленных отверстий цилиндрической или конической формы. С помощью зенковки, при выборе необходимого типа инструмента, можно получить различные по конфигурации углубления в отверстиях обрабатываемых деталей. Не следует путать зенковку с зенкерованием, рассверливанием отверстий на всю длину для повышения качества поверхности.
Виды и применение зенковок
При обработке деталей на сверлильных и токарных станках зенковка по металлу применяется для:
- Формирование в предварительно подготовленных отверстиях углублений конической или цилиндрической формы требуемой длины.
- Формирование опорных плоскостей возле отверстий.
- Съём фаски в отверстиях.
- Обработка отверстий под крепеж.
Часто можно встретить и термин «цековка», так называют инструмент, предназначенный для рассверливания углублений цилиндрической формы и опорных плоскостей.
По конфигурации режущей части встречаются следующие виды зенковок:
- Цилиндрической конфигурации.
- Конические зенковки.
- Торцовые инструменты.
По диаметру обрабатываемых отверстий зенковки подразделяются на:
- Простые (от 0,5 до 1,5 мм).
- Для отверстий диаметром от 0,5 до 6 мм. Выпускаются с предохранительным или без предохранительного конуса.
- Зенковки с конусным хвостовиком. Применяются для отверстий диаметром от 8 до 12 мм.
Конструкция
Зенковка коническая состоит из двух основных элементов — рабочей части и хвостовика. Рабочая часть имеет конус со стандартным рядом углов на вершине от 60 до 120°. Количество режущих лезвий зависит от диаметра инструмента и может быть от 6 до 12 штук.
Цилиндрическая зенковка по своей конструкции похожа на сверло, но имеет больше режущих элементов. На торце расположена направляющая цапфа необходимая для фиксации положения инструмента в процессе обработки. Ограничитель может быть съёмным или быть часть тела инструмента. Первый вариант более практичен, так как расширяет возможности обработки. Также может быть установлена режущая насадка.
При необходимости рассверливания нескольких отверстий на равную глубину применяется инструмент с державками с вращающимся или неподвижным ограничителем. Перед обработкой зенковка фиксируется в державке таким образом, чтобы режущая часть выступала из упора на расстояние равное требуемой глубине обработки отверстий.
Инструмент изготавливается из инструментальных легированных, углеродистых, быстрорежущих и твердосплавных марок стали. Для обработки чугунных деталей чаще всего используются твердосплавные стали, для обычных сталей – быстрорежущие и инструментальные.
Особенности зенкования отверстий
Приведём некоторые рекомендации для металлообработки методом зенкования:
- При обработке твердых сплавов и чугуна необходимо использовать охлаждающие эмульсионные составы для отвода тепла.
- Очень важно правильно подобрать инструмент для проведения работ. Необходимо учесть материал заготовки и характер работ.
- При подбое зенковки особое внимание уделите заданным параметрам обработки – диаметр, потребная точность, размер углубления.
- Обратите внимание на способ фиксации на станке, при необходимости приобретите необходимую дополнительную оснастку.
Действующий ГОСТ
Определяет технические условия для конической зенковки ГОСТ 14953-80. Также, при металлообработке, следует руководствоваться другими стандартами регулирующими параметры используемых сходных инструментов – зенкеров, разверток и т. д. Подбор зенковок необходимо производить по таблицам в специальной литературе.
что это, ГОСТы, виды и элементы
Зенкер по металлу применяют в машиностроении, там, где необходимо проводить обработку высверленных отверстий, а именно – выравнивать канал. Рассмотрим элементы инструмента, его виды и параметры.
Сверление отверстий в металле ответственных изделий требует высокой точности. Образованный канал должен строго соответствовать необходимому диаметру. Получить такой результат только одним сверлом сложно: даже незначительное биение приводит к погрешности. Поэтому прецизионное сверление проводят в два этапа: вначале применяют сверло, а после – зенкер по металлу.
Под зенкером понимают специальный инструмент, который имеет несколько лезвий. С помощью него можно делать расширение готового отверстия либо чистовую проточку. Если у сверла рабочая режущая часть расположена на торце, то у зенкера резцы идут по спирали вдоль всего тела. Его работа схожа с работой фрезы, то есть он при вращении срезает тонкий слой металла в высверленном канале.
Операция обработки металла зенкером называется зенкерованием. Бывают разные типы зенкеров, некоторые из них внешне похожи на сверло по металлу, особенно те, которые имеют цельную конструкцию.
Для качественной обработки отверстий не следует применять обычную ручную электродрель – только сверлильный или токарный станок!
Классификация зенкеров и их назначение
Зенкер был разработан для машиностроения и применяется в основном в операциях металлообработки. Бывают разные виды зенкеров – все они используются в определенных технологических процессах. Классификация инструмента идет в первую очередь по двум основным группам:
- К первой группе относятся элементы разных видов и конструкций, основным назначением которых является промежуточный этап обработки, за ним следуют припуск и развертывание.
- Во вторую группу входят инструменты, предназначенные для финишной обработки отверстий в металле с точностью, что соответствует 4 и 5 классу (Н11 – квалитет).
Имеются отличия по конструкции. В этой категории бывают следующие виды инструмента:
- Цельнометаллический элемент, где режущая рабочая часть и хвостовик выполнены на одном металлическом стержне.
- Сборный элемент – зенкер насадной, который надевается на стержень направляющей. В качестве направляющей может быть продолжение хвостовика или специальное сверло. Суть в том, что можно объединить разные по диаметру элементы на одном инструменте, если отверстие сложное и имеет несколько диаметров.
- Зенкер сварной.
- Инструмент, в котором имеются твердосплавные режущие пластины.
Также есть отличия по форме рабочей зоны. Это такие виды инструмента:
- Элементы с рабочей областью в форме цилиндра. Их основное назначение – расширять отверстия методом зенкерования.
- Элементы с цилиндрической рабочей областью, где имеется направляющая цапфа. Эта конструкция используется для обработки отверстий под крепежные метизы.
- Зенкеры конической формы необходимы, если нужно образовать коническое углубление в начале отверстия.
- Элементы с рабочей областью на торце инструмента позволяют проводить зачистку торцевых плоскостей приливов, бобышек.
Особенности конических зенкеров
Зенкер конический применяют для операций зенковки металла. Этот технологический процесс предполагает снятие фаски в отверстии или получение конического углубления в металле. Самый распространенный и доступный для использования элемент конической формы – это инструмент типа ВК8. Его диаметр бывает разным в пределах 15–75 мм. Целевое назначение – создание конических поверхностей в начале отверстий с высоким классом точности. При этом заглубление получается незначительным, а угол обработки – средним.
- резцы зенкования на небольшую глубину – основание у них цилиндрическое и продолговатое;
- резцы зенкования на небольшую глубину и зенкования материалов листовой стали – основание у них коническое с узкой цилиндрической юбкой;
- резцы для зенкования на большую глубину – основание узкое, цилиндрическое, с небольшим углом к хвостовику.
Получение необходимого углубления в отверстии коническим зенкером предполагает, что во время сверления нужно обеспечить припуск 2–3 мм. Сам процесс обработки осуществляется посредством применения станка для токарных работ, в патрон которого он крепится. Деталь выставляют отверстием напротив резца в строгом соблюдении осей. Рабочая часть инструмента подается к заготовке в ручном режиме.
При работе зенкером в область обработки необходимо подавать материалы, служащие для охлаждения и смазки. В такой процедуре не нуждаются только элементы с твердосплавными напайками!
Геометрические параметры
Чтобы правильно подобрать зенкер под конкретную задачу, нужно знать, с каким металлом он будет работать и что за параметры имеют основные элементы зенкера. Для цельнометаллических элементов цилиндрической формы предусмотрены следующие стандарты на геометрические параметры при обработке конкретных материалов:
- У деталей, выполненных из стали конструкционного назначения с отверстиями до 40.0 мм в диаметре, обработку последних проводят инструментом с диаметром рабочей части от 40 до 10 мм и количеством режущих кромок 3–4 единицы. Если диаметр достигает 80 мм, то резец должен быть в пределах 32–80 мм.
- У деталей, выполненных из металла, который был подвержен закалке, отверстия обрабатывают 4- и 3-лезвийными зенкерами с размером поперечного сечения от 50 до 14 мм.
- У деталей из чугуна либо металла цветного операцию зенкерования для глухих отверстий проводят перовым инструментом.
Рекомендации по применению конических элементов к типу металла, что должно соответствовать определенной геометрической форме конуса (имеется в виду угол), следующие:
- От 20 до 15 градусов угол можно применять, когда необходима обработка мягких марок стали и сплавов.
- От 10 до 8 градусов угол подойдет для работы, что предполагает зенковку металлов с твердостью средней величины либо деталей для отливок стальных.
- Угол в 5 градусов и ниже применим для зенковки заготовок из чугуна либо сталей высоколегированных.
Когда при помощи зенкера проводят чистовую обработку изделия, диаметр поперечника инструмента должен совпадать с тем диаметром, который должен получиться в итоге!
Действующие ГОСТ
Зенкер – высокоточный инструмент. Все его геометрические размеры, углы режущей кромки в коническом элементе, форма спирали лезвия, количество лезвий строго оговорены нормами стандартизации в ГОСТ. Так, действующие сегодня документы по разным видам зенкеров следующие:
- ГОСТ 14953-80 описывает условия (технические) применения элементов с конической формой рабочей зоны. Здесь указаны геометрические параметры, материал, из которого изготовлен инструмент, металл, с которым может работать конкретный элемент.
- ГОСТ 12489-71 касается такого инструмента, как цельный зенкер цилиндрической формы.
Уважаемые посетители сайта, кто владеет информацией, касающейся темы, поддержите обсуждения в комментариях!
Зенкеры, зенкерование и зенковки. Виды зенковки.
В современных технологиях по производству изделий или деталей, особое место занимает обработка отверстий. Это довольно сложный и ответственный технологический процесс, в котором необходимы специальные инструменты. Это, в основном, металлорежущие инструменты, предназначенные для промышленного применения станочного и ручного типа. Для выполнения отверстий пользуются сверлами. А для обработки подготовленных сверлами отверстий применяются зенковки и зенкеры.
Зенкер (нем. senker), относится к металлорежущим инструментам, использующимся для предварительной и окончательной обработки стенок отверстий. Такой вид работ по металлу называется зенкерованием. Зенкер, в отличие от сверла, оснащен большим числом режущих кромок (от 3 до 6, есть и больше). Часто, при выполнении зенкерования, используют смазочно-охлаждающие вещества (СОЖ).
Материалы, из которых изготавливаются зенкеры, должны быть более прочными и износостойкими, чем обрабатываемый материал, обычно высокопрочные металлы и сплавы.
Основные виды зенкеров:
- Машинные цельные, с коническим хвостовиком. Предназначены они для предварительной обработки отверстий конической формы.
- Насадные, которые по своей сути являются насадками, имеют напаянные пластины из твердого сплава. Предназначены для окончательной обработки стенок отверстия в чугунных и стальных деталях.
Зенкерование выполняют на различных металлообрабатывающих станках:
- Токарные
- Сверлильные
- Фрезерные с ЧПУ
- Расточные
- Агрегатные
Зенковка-это металлорежущий, многолезвийный инструмент. Она используется для выполнения отверстий различной формы и величины. Также зенковка используется для корректировки уже подготовленных отверстий, для выполнения опорных поверхностей вокруг отверстий. Отличаются зенковки от зенкеров тем, что имеют направляющие цапфы и зубья на торцах.
Зенковки делятся по форме режущей части на следующие виды:
- Цилиндрические. Имеют направляющую цапфу для обеспечения соосности.
- Конические. Имеют направляющую цапфу для обеспечения соосности.
- Торцовые, используют для зачистки внешней поверхности под потайные головки крепежных инструментов.
Так как зенковки изготавливаются по определенным стандартам, то они делятся по диаметру отверстий, которые обрабатывают:
- Простые (от 0,5 до 1,5 мм)
- С предохранительным конусом или без него (от 0,5 до 6 мм)
- С конусным хвостовиком (от 8 до 12 мм)
Зенкование осуществляется на металлообрабатывающих станках:
- Сверлильных
- Токарных
- Токарно-револьверных
- Агрегатных
Оба процесса, и зенкерование и зенкование, близки по значениям в режимах работы. Они осуществляются на одинаковых видах оборудования. Оба метода обработки могут найти применение в условиях единичного, серийного и массового производства.
Чем отличается зенкование от зенкерования — сверление, инструмент, особенности зенкования
Зенкование и зенкерование, несмотря на схожесть названий, являются разными операциями металлообработки с соответствующим инструментом. Схожесть операций в типе обработки и обрабатываемой поверхности. И зенкование, и зенкерование подразумевает механическую обработку резанием внутренней поверхности отверстий. Различия в характере обработки и, соответственно, получаемом результате.
Зенкерование: инструмент и особенности
Зенкерование – это промежуточный процесс обработки отверстий располагаемый, как правило, между сверлением и разверткой. Это получистовая обработка отверстия с целью:
- повышения точности отверстия до 4-го и даже 5-го класса;
- улучшения шероховатости;
- придания строгой геометрической формы.
Также зенкерование применяется при обработке отверстий полученных литьём или обработкой давлением.
Обработка производится с помощью зенкера, инструмента внешне похожего на сверло, но имеющего ряд конструктивных отличий. Основные отличия – это увеличенная перемычка между режущими кромками, увеличенное количество рабочих кромок и срезанный угол. Всё это обеспечивает высокую устойчивость зенкера и его соосность с обрабатываемым отверстием. Так, наличие 3-4 режущих кромок обеспечивает плавное распределение сил в зоне контакта зенкера с обрабатываемой деталью. Геометрия режущей части обеспечивает обработку отверстия без съема металла в продольном направлении.
Зенкеры различаются по количеству зубьев (3 или 4) и конструкции – насадные, цельные и вставные. Выбор инструмента зависит от диаметра отверстия. Так, применение вставных зенкеров (с вставными ножами) рекомендуется для отверстий диаметром от 20 мм., цельные применяются для малых диаметров (от 12 мм.).
Для получения более точных и сложных поверхностей используются комбинированные типы инструмента с большим количеством режущих кромок (до 8). При этом сборные зенкеры применяются совместно с другим металлорежущим инструментом – сверлами, развертками и т. д.
Особенности зенкования
Зенкование – это механическая обработка отверстий с целью создания различных геометрических углублений для потайного размещения крепежных изделий. Также она применяется для нарезки внутренних фасок. Для этих целей есть специальный инструмент – зенковка, имеющие различную форму. Выбор зенковки зависит от необходимого конечного результата.
Основные виды зенковок
- Цилиндрические зенковки. Применяются для получения цилиндрических выемок в просверленных отверстиях под установку болтов и винтов.
- Конические зенковки. Используются для вырезания отверстий конусной формы внутри детали, а также для зачистки острых кромок, снятия фасок и подготовки углублений под крепежные элементы. Чаще всего применяется инструмент с конусным углом 90° и 120°.
- Плоские или торцевые зенковки, также можно встретить название цековки. Преимущественно применяются для зачистки и обработки углублений перед установкой крепежных изделий.
Зенковка состоит из рабочей части и хвостовика со специальной цапфой выполняющей функцию направляющего пояса. Цапфа необходима для контроля соосности в процессе нарезки углублений.
Оборудование
Для зенкования и зенкерования используется, чаще всего, сверлильные станки различного типа. Также может быть использован обрабатывающий центр или токарный станок – практически тоже самое оборудование, на котором выполняются и операции сверления. Для обеих операций не рекомендуется использовать ручной инструмент из-за недостаточной точности позиционирования.
IV. Зенкеры, их назначение, виды и конструкция.
Зенкеры предназначаются для обработки цилиндрических отверстий: необработанных (литых и штампованных) и предварительно просверленных с целью улучшения чистоты поверхности и повышения точности этихотверстий, а в ряде случаев и подготовки их к дальнейшему развертыванию. При обработке отверстий, полученных литьем, ковкой или штамповкой, применяют зенкеры, а не сверла, т.к. при работе по корке они более устойчивы. Среднее значение припуска под зенкерование после сверления составляет примерно 0,5…3 мм на сторону.
По форме режущей части зенкер напоминает спиральное сверло, но в отличие от сверла он имеет не две, а три или четыре главные режущие кромки, расположенные на режущей части; кроме того, зенкер не имеет поперечной кромки. По сравнению со сверлом зенкер обладает повышенной жесткостью и благодаря наличию нескольких режущих лезвий имеет хорошую ориентировку относительно уже сделанного отверстия, поэтомуэтот тип инструмента применяют часто для исправления геометрии отверстия (получение цилиндричности).
Цилиндрический зенкер имеет следующие основные части ( см. рис.7):режущая (заборная) часть, несущая режущие кромки. Эта часть инструмента выполняет основную работу резания;калибрующая (направляющая) часть, имеющая узкие фаски и служащая для направления зенкера в отверстии в процессе резания;хвостовик, служащий для закрепления зенкера в шпинделе станка.
Рис. 7. Элементы и части цилиндрического зенкера.
Рис. 8. Разновидности цельных зенкеров.
Для обработки цилиндрических поверхностей применяются цельные зенкеры: с прямыми канавками (рис.8,а), с винтовыми канавками (рис. 8,6), с напаянными твердосплавными пластинами (рис. 8,в). Эти три типа зенкеров можно использовать для обработки отверстий как ручным способом, так и с помощью металлорежущего оборудования. Зенкер, изображенный на рис. 8,г применяется только при обработке на станках (вследствие неразвитой направляющей части) и называется машинным
На рисунке 9 показаны различные виды насадных зенкеров, которые закрепляются на оправке станка и вручную не используются: с напаянными твердосплавными зубьями (рис.9,а), со вставными зубьями (рис. 9,6) и цельный (рис. 9, в.)
Для обработки входной или выходной части отверстия с целью снятия фаски или для изготовления углубления под головку болта, винта или заклепки используется операция зенкования, которая выполняется зенковками (см. рис. 10).
а) б) в)
.
Рис. 9. Насадные зенкера
Рис. 10. Разновидности зенковок
V. Развертки, их назначение, виды и конструкция.
Развертка (рис. 11) — многолезвийный инструмент, предназначенный для чистовой обработки отверстий обычно после зенкерования. Число лезвий составляет от 6 до 12. После операции развертывания получается низкая шероховатость поверхности (высокая чистота) и достаточно точный размер ( по 6…8 квалитету). Припуск под обработку составляет 0,05.. .0,3 мм на сторону.
Рис. 11. Элементы цилиндрической развертки.
Развертывание отверстий можно выполнять на сверлильных или токарных станках, а также вручную. Развертки, применяемые для станочного развертывания отверстий, называются машинными (см. рис. 12).
Рис. 12. Виды машинных разверток.
Машинные развертки отличаются от ручных более короткой рабочей частью. Они закрепляются в качающихся (плавающих) державках, установленных в патроне или непосредственно в шпинделе станка. Ручная развертка, не имеющая возможность быть сцентрированной на станке, имеет длинную заборную часть, благодаря которой инструмент имеет возможность самостоятельно центрироваться по отверстию. На рисунке 13,а показана ручная цилиндрическая развертка с прямым зубом, на рисунке 13,6 — с. винтовым зубом и на рисунке 13,в — ручная коническая развертка с прямым зубом
а) б) в)
Рис. 13. Разновидности ручных разверток.
Конические развертки применяются для предварительного и окончательного развертывания конических поверхностей. Обычно такие развертки состоят из комплекта (см. рис. 14), первая — черновая (рис. 14,а) — обращает цилиндрическое отверстие в ступенчатое. Промежуточная коническая развертка (рис. 14,6) предназначена для раздробления стружки и придания отверстию более правильной конической формы. Последняя — чистовая развертка (рис. 14,в) — снимает стружку по всей режущей кромке конуса.
Рис. 14. Комплект конических разверток.
По своему устройству развертки делятся на две больших группы: постоянные и регулируемые. На рисунке 15 показана цилиндрическая регулируемая развертка. Корпус такой развертки сделан полым коническим, с продольными канавками, прорезанными между зубьями на длине рабочей части. При завертывании винта, расположенном с торца развертки, шарик, расположенный внутри, продвигаясь по внутренней конической поверхности, «распирает» тело инструмента, тем самым изменяя наружный диаметр.
Рис. 15. Регулируемые ручные развертки.
Для получения отверстий идеальной цилиндрической формы с низкой шероховатостью поверхности применяется растачивание. В качестве инструмента используется обычно расточный резец (рис. 16). Операция растачивания может производиться на станках токарной группы, расточных станках и на координатно-расточных.
Для нарезания резьбы
в отверстиях применяются метчики. Метчик
— режущий инструмент,
представляющий собой закаленный винт,
на котором прорезано несколько
продольных канавок (прямых или винтовых),
образующих режущие кромки (рис.
16). Метчик имеет рабочую часть и хвостовик,
заканчивающийся квадратом. Рабочая
часть метчика состоит из заборной и
калибрующей частей. Заборная
часть — передняя
конусная часть метчика, которая первой
входит в отверстие и осуществляет
всю основную работу резания. Калибрующая
часть направляет
метчик в отверстие и окончательно
калибрует резьбу.
Ручные метчики — служат для нарезания резьбы вручную. Они обычно изготавливаются комплектами из двух или трех метчиков. В комплект, состоящий из трех метчиков, входят черновой, средний и чистовой метчики.
Машинно-ручные метчики применяются для нарезания цилиндрической и конической резьбы в сквозных и глухих отверстиях. Этими метчиками можно нарезать машинным способом резьбы всех размеров и вручную
Рис. 16. Ручной метчик и его элементы.
для чего нужен и что с ним делать?
Для обеспечения точности параметров обрабатываемых отверстий требуется зенкерование. Без специального инструмента тут не обойтись. С этой целью используется зенкер по металлу, а для чего он нужен, и что с ним делать, можно узнать из этого материала.
Для чего нужен зенкер по металлу, и как правильно его использовать? Можно ли сделать инструмент своими руками?
Назначение инструмента и разновидности
Зенкер по металлу – это высокоточный многогранный инструмент с заострением на конце. Применяется в технологических процессах при необходимости обеспечения точности в отверстиях, имеющих форму круга. Смысл заключается в увеличении качественной характеристики поверхности.
Этот производственный процесс именуется зенкерованием. Он идентичен обработке сверлением, так как применяемый инструмент с заданными параметрами вращается вокруг своей оси и продвигается в глубину заготовки, все это происходит одновременно.
Зенкер был изначально предназначен для металлообработки, применяемой в машиностроении для получения точности после штамповки, отливки, сверления или долбления. И на сегодняшний день зенкер используют в техпроцессах машиностроительной сферы.
► Его применяют в:
- Промежуточных операциях.
- Чистовых обработках.
► Технологический инструмент подразделяется на :
- для развертывания с обеспечением припуска или обработки разверткой – №1;
- 4 или 5 допуском (11 квалитетом) – № 2.
При расточке отверстия его диаметр увеличивается, и чистота обработки повышается.
► Технические характеристики процесса:
- Очистка обрабатываемой поверхности или сглаживание неровностей.
- Калибровка отверстий под крепежные элементы.
- Обработка торцов поверхностей.
- Придания профиля или расширение на глубину, к примеру, под болтовые головки.
► Различают инструмент также по способам крепежа в станочном оборудовании:
- С конусом Морзе хвостовой или с метрическим конусом (так именуются конструктивные элементы крепления в технологическую оснастку).
- С конструктивным элементом-насадкой.
► По конструкторскому исполнению зенкера, согласно требований ТУ или ГОСТ подразделяются на:
- Цилиндрические. Изготовлены из износоустойчивых металлов, производятся диаметром от 10 до 20 мм.
- Зенкер конический цельный. Изготовление производится из быстрорежущих и легированных металлических материалов, покрытие износоустойчиво. Размеры в диаметре от 10 до 40 мм.
- Инструмент цельный насадной, диаметр в диапазоне от 32 до 80 мм.
- Зенкер конусный исходя из стандартных требований производится типов 1 или 2, и насадной. На таком инструменте имеются пластины из твердых сплавов.
- Соединенные сваркой.
- Оснащенные пластинами из твердых сплавов.
Зенкер можно сделать самостоятельно, если имеются необходимые заготовки, и применять такой инструмент в случаях, если не требуется особой точности при обработке.
Разница между зенкерованием и смежными операциями
Зенкерование напоминает сверление, только выполняется в подготовленные технологические отверстия. При данной операции получается более точный результат, так как некоторые погрешности устраняются, выправляется соосность, увеличивается точность и чистота обработки.
В процессе сверления инструмент может отклониться от оси, особенно когда большая глубина. Зенкерование выполняется инструментом, обладающим высокой жесткостью, так как число режущих кромок большое, что обеспечивает точность и заданное направление. При низких глубинах резки обеспечивается еще большая точность.
Для сравнения можно привести пример: при рассверливании получаемая шероховатость – Rz 20мкм и 11-12 – это квалитеты, при обработке зенкером – шероховатость Ra 20мкм, 9-11 квалитеты. Сверло по металлу 85, изготовленное в соответствии с ГОСТ, используется в металлообработке при необходимости выполнения кольцевого сквозного отверстия.
Имеются инструменты, имеющие комбинированное исполнение, к ним относится сверло-зенкер. Применяется с особо ответственных техпроцессах при обработке металлов резанием.
Развертывание проводится после операций сверления и зенкерования отверстий, относимое к более точной механической обработке. Инструмент-развертка. Последнее относиться к получистовой операции, и в этом заключается отличие зенкерования от развертывания.
Зачастую происходит путаница между зенковкой и зенкером. Зенковка нужна для снятия фасок с отверстий, либо необходимости получения фасок конической конфигурации под заклепки, винты или болты. Эта операция называется зенкованием. Зенковки – это многолезвийный инструмент, выполняемый по нормам ГОСТ. Подразделение осуществляется по нескольким видам:
- Коническая, имеющая угол 60 градусов, 90 и 120. Используется для обеспечения фасок под крепежи или метизы.
- Цилиндрическая, имеющая хвостовик и износоустойчивое покрытие. Применяется в техпроцессах при обработке опорных заготовок.
Отверстия под потайные головки крепежных элементов можно производить цековкой. Это инструмент для резки металла для получения цилиндрических отверстий, под фаски болтов, заклепок, а также для опорных поверхностей.
Тонкости правильного зенкерования металлических заготовок
При выполнении зенкерования углублений в металле для заготовок, не требующих высокой точности, используется простое сверло, закрепленное к патрону обычной дрели. Такое практикуется в домашнем хозяйстве. При выполнении серьезных технологических операций в машиностроительных отраслях эта работа требует большой мощности и соответствующего оборудования.
Поэтому при таком подходе применяются:
- Расточное оборудование.
- Сверлильные установки.
- Токарные станки.
- Агрегатное (используемое для повторной обработки на оснащенной автоматикой линии).
- Фрезерные станки.
Зенкерование отверстия после отливки рекомендуется выполнить его растачивание на от 5 до 10 мм в глубину. Это необходимо, что зенкер принял заданные координаты.
При выполнении обработки стальных изделий применение смазочно-охлаждающих жидкостей обязательно, так как металл сильно нагревается и становится мягким, а это влияет на качество обработки. При обработке изделий из цветного металла не требует применения СОЖ, они наиболее податливы к внешним воздействиям и обработка отверстий выполняется быстрее.
► При выборе инструмента требуется руководствоваться следующими нюансами:
- Тип применяемого инструмента выбирается на основании материала обрабатываемой заготовки. При этом немаловажно учитывать расположение отверстия и серийность производства.
- Исходя из заданных параметров точности, диаметра и глубины обработки производят соответствующий выбор зенкера.
- Способ крепления в станочном приспособлении немаловажен при выборе.
- Материал, из которого выполнен инструмент, зависит от материала детали, Например, это может быть зенкер по металлу или по дереву.
В помощь при выборе инструмента имеют место быть государственные стандарты, а именно ГОСТ 12489-71 будет настольной книгой в этом деле. Инструмент должен соответствовать ТУ и ГОСТ.
► Примеры правильно выбора:
- Для изделий, материалом которых является конструкционная сталь, и при этом есть необходимость получить отверстие до 40 мм по диаметру, производится обработка зенкером из быстрорежущей стали. Сам инструмент должен иметь 3 или 4 зуба, а диаметр не менее 30 и не более 40 мм.
- Если изделие выполнено из закаленной или иной труднообрабатываемой стали, то при его расточке необходимо сделать выбор в пользу инструмента с твердосплавными пластинами. При этом показатели диаметра выбираются в пределах от 40 до 50 мм, а количество зубьев от 3 до 4.
- Перед обработкой изделий из конструкционных материалов стали при обработке отверстий до 80 мм в диаметре, растачивание производится зенкером из быстрорежущего материала с использованием насадных головок диаметром от 32 до 80 мм.
- Перовой зенкер используется для обработки заготовок из чугуна и цветного металла.
- При обработке глухих отверстий, диаметр которых колеблется в пределах 15-25 мм обработка, происходит специальным инструментом, имеющим в корпусной части канал для подачи СОЖ.
Для выполнения качественных работ по зенкерованию необходимо соблюдать припуски. Параметры диаметра применяемого инструмента должны соответствовать с размером полученного диаметра в заготовке после технологической операции.
В случае если после зенкерования необходимо будет исполнение развертывания, то инструмент должен быть выбран из расчета на 0,15 или на 0,3 мм меньше, чем получаемый в результате размер. При нанесении метки черновой расточки ли сверления в качестве подготовки для зенкерования следует выполнять припуск на сторону размером от 0,5 до 2 мм.
Видео: свёрла, зенковки.
Охрана труда
При непосредственном выполнении производственных задач не нужно забывать и о собственной безопасности, при этом неважно какой инструмент применяется сверло, зенкер или зенковка.
Перечень правил и рекомендаций:
- Работать в специальной одежде, при этом не должно быть свивающих ниток и обрывков ткани, пуговицы следует все застегнуть.
- Обувь должна быть закрытого типа, к таковой относятся ботинки или сандалии, специально изготовленные. В сланцах работать нельзя.
- Защитный экран для обеспечения защиты всего лица от возможного попадания стружки.
- Головной убор обязателен.
- Во время вращения патрона в перчатках работать нельзя.
- Перед работой необходимо проверить наличие заземляющего устройства и целостность провода заземления.
- Производить осмотр инструмента на наличие трещин, сколов и заусениц во избежание получения травмы.
Если на рабочем месте, по мнению работника, имеются требований ОТ и ТБ, то следует об этом доложить руководству и приступать к работе только после получения разрешения.